Facility design
Who we are
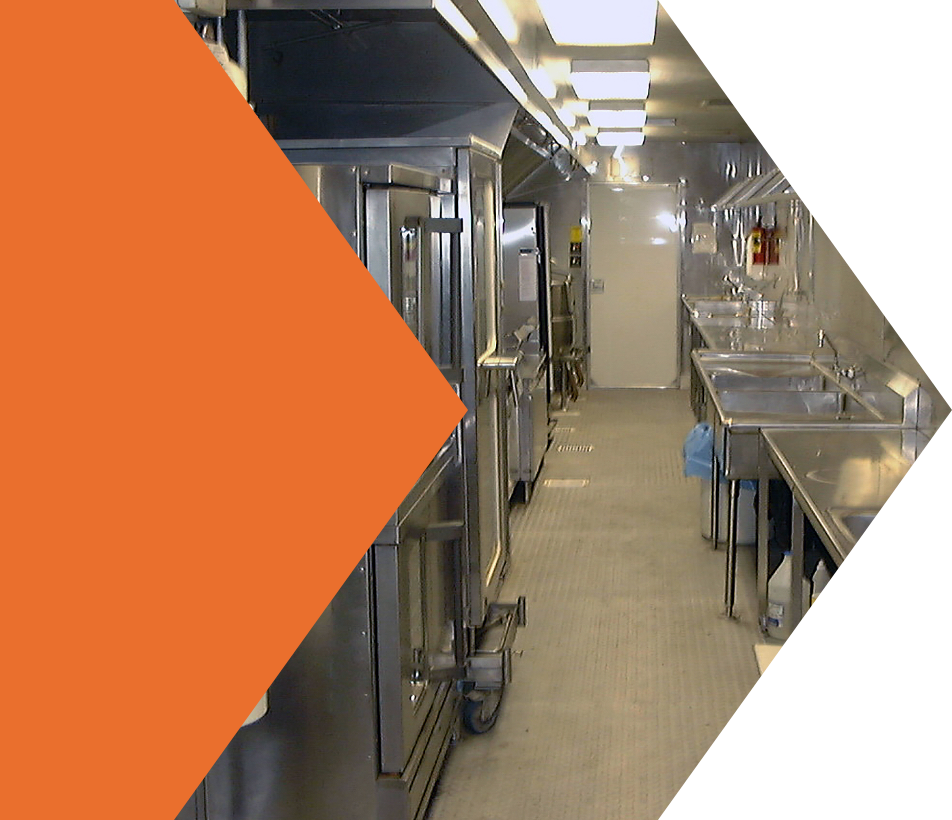
our projects
From concept to completion, including equipment specification, procurement, inspection, testing and commissioning, we have decades of experience and a portfolio of successful projects.
past projects
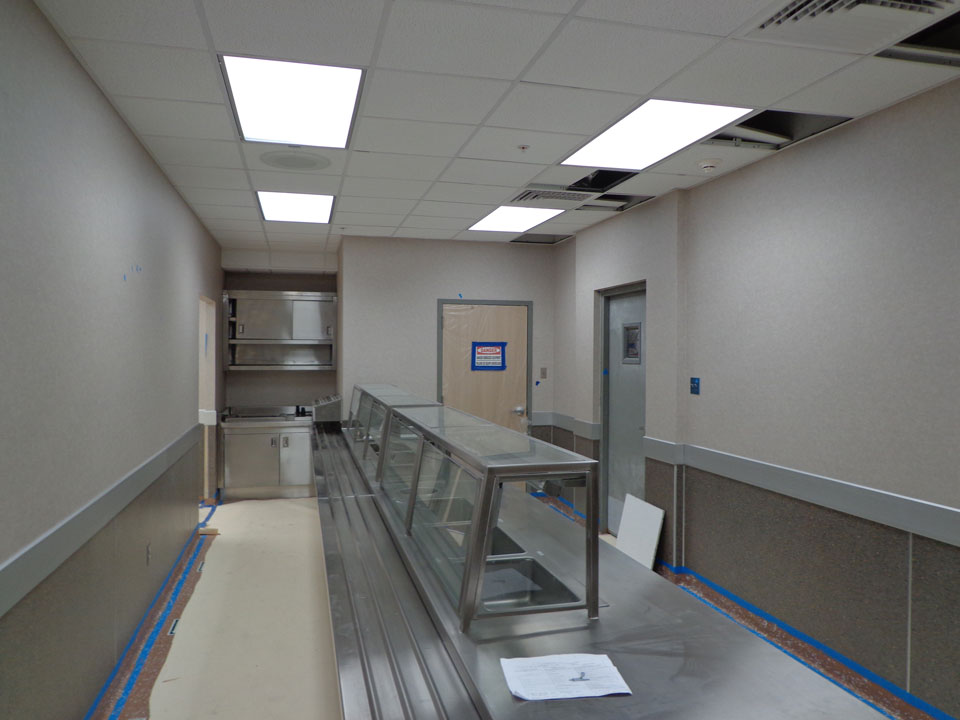
We worked with Shell from design to commissioning. Photos show the platform in the shipyard under construction.
Olympus
Gulf of Mexico
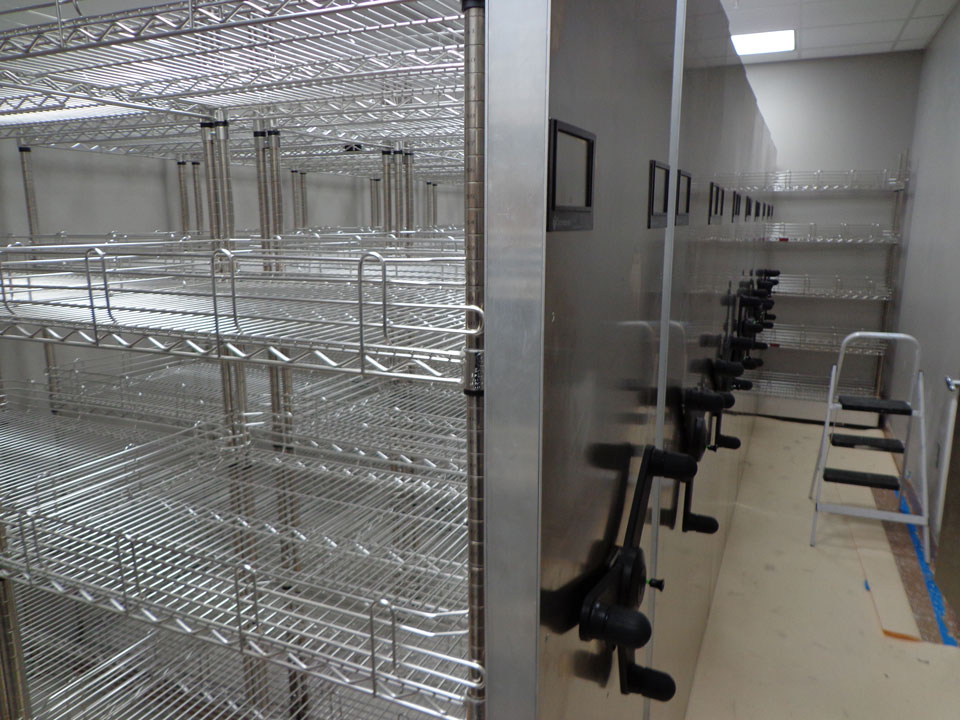
We worked with Shell from design to commissioning. Photos show the platform in the shipyard under construction.
Olympus
Gulf of Mexico
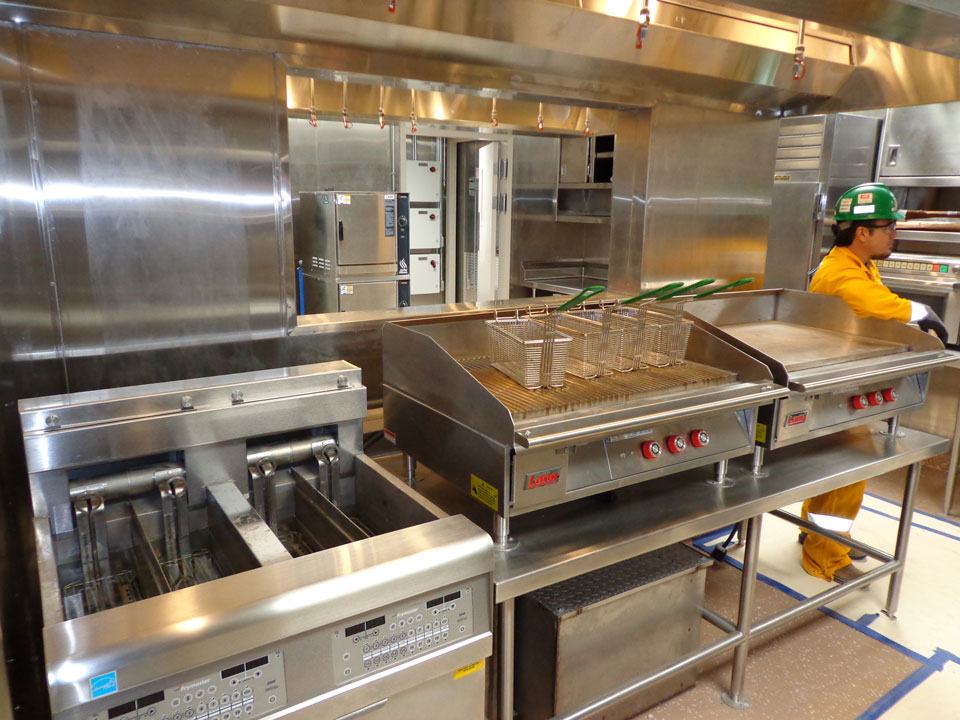
We worked with Shell from design to commissioning. Photos show the platform in the shipyard under construction.
Olympus
Gulf of Mexico
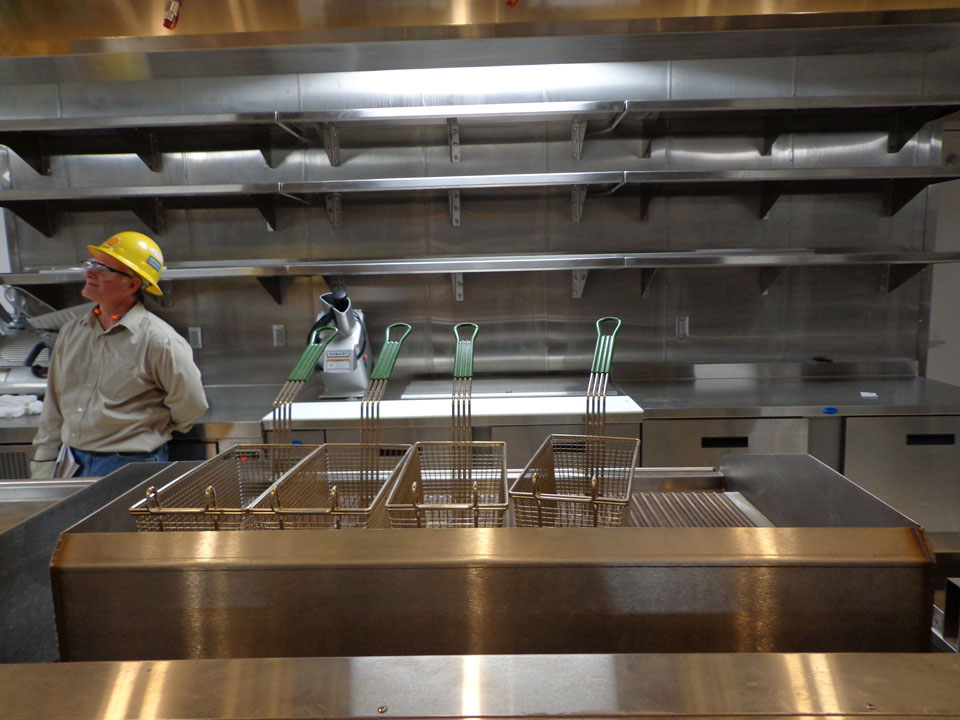
We worked with Shell from design to commissioning. Photos show the platform in the shipyard under construction.
Olympus
Gulf of Mexico
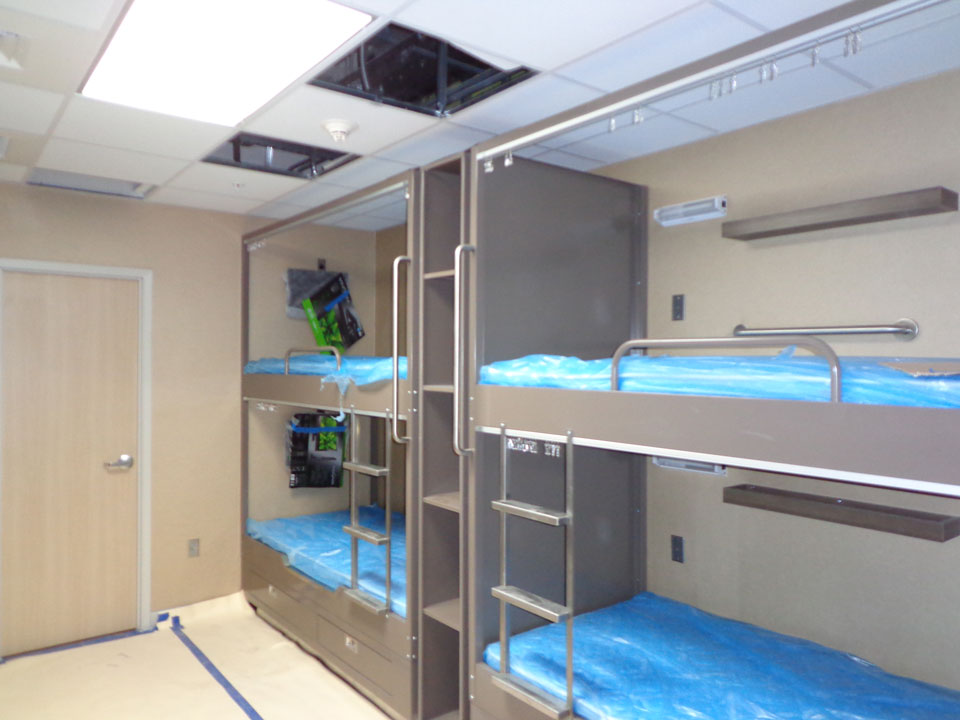
We worked with Shell from design to commissioning. Photos show the platform in the shipyard under construction.
Olympus
Gulf of Mexico
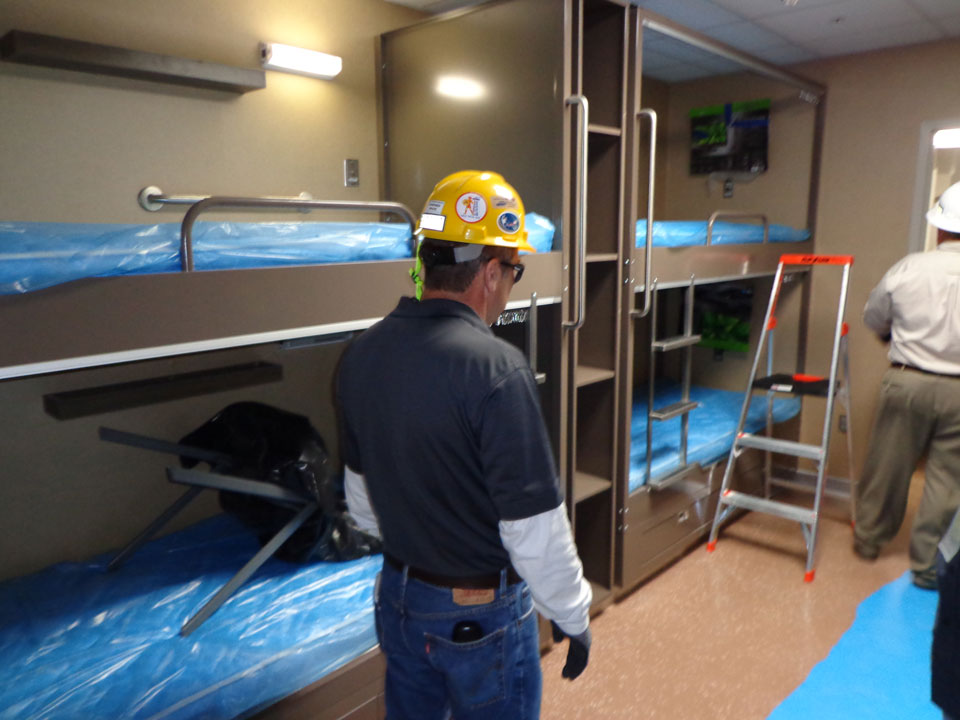
We worked with Shell from design to commissioning. Photos show the platform in the shipyard under construction.
Olympus
Gulf of Mexico
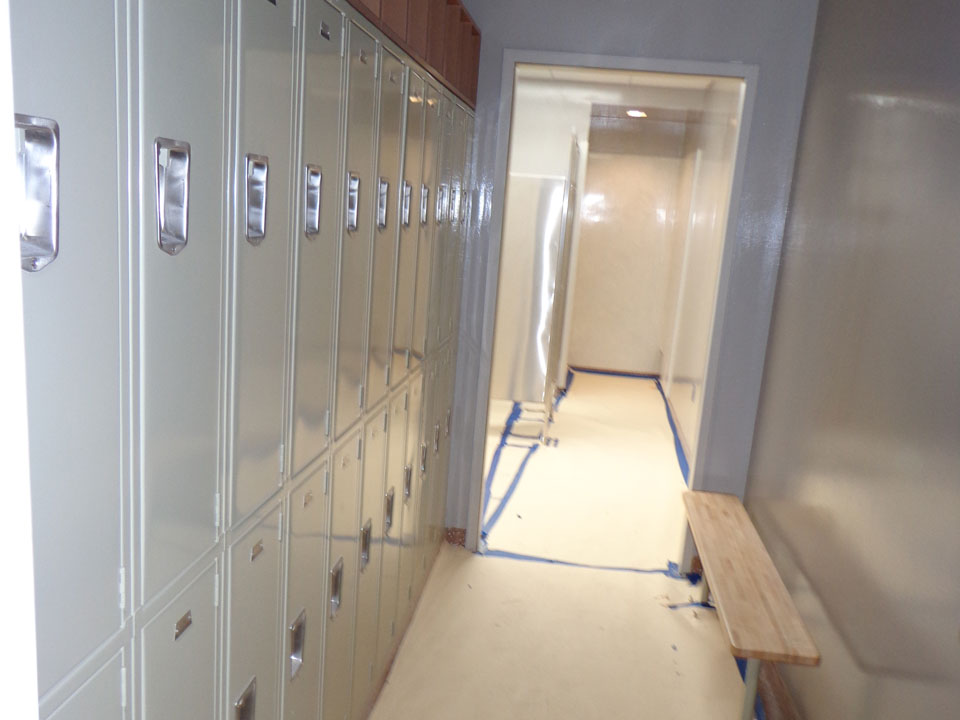
We worked with Shell from design to commissioning. Photos show the platform in the shipyard under construction.
Olympus
Gulf of Mexico
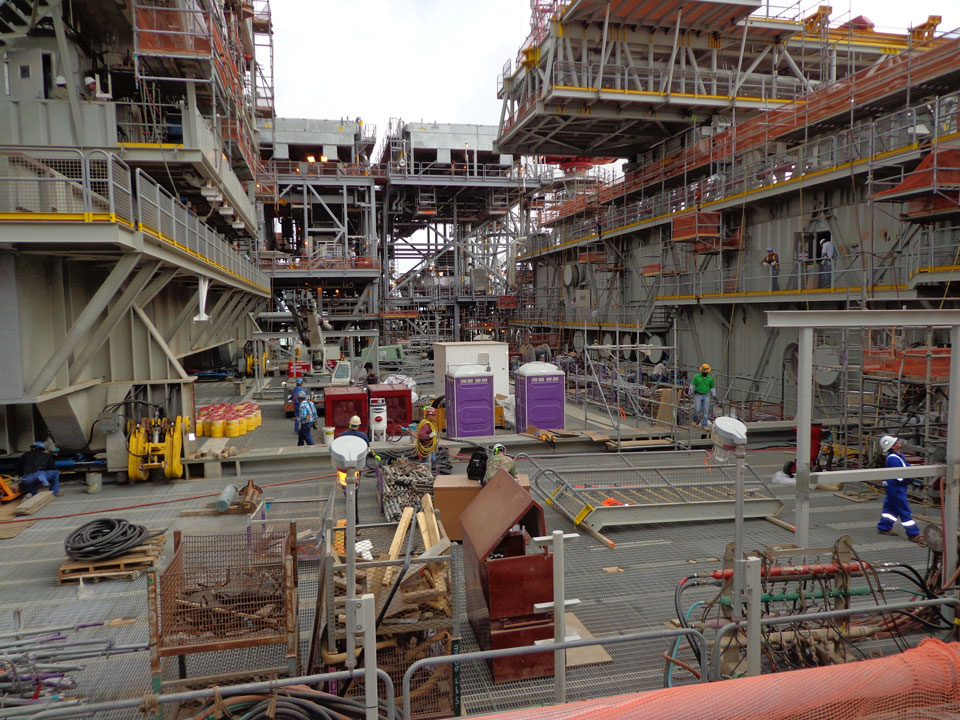
We worked with Shell from design to commissioning. Photos show the platform in the shipyard under construction.
Olympus
Gulf of Mexico
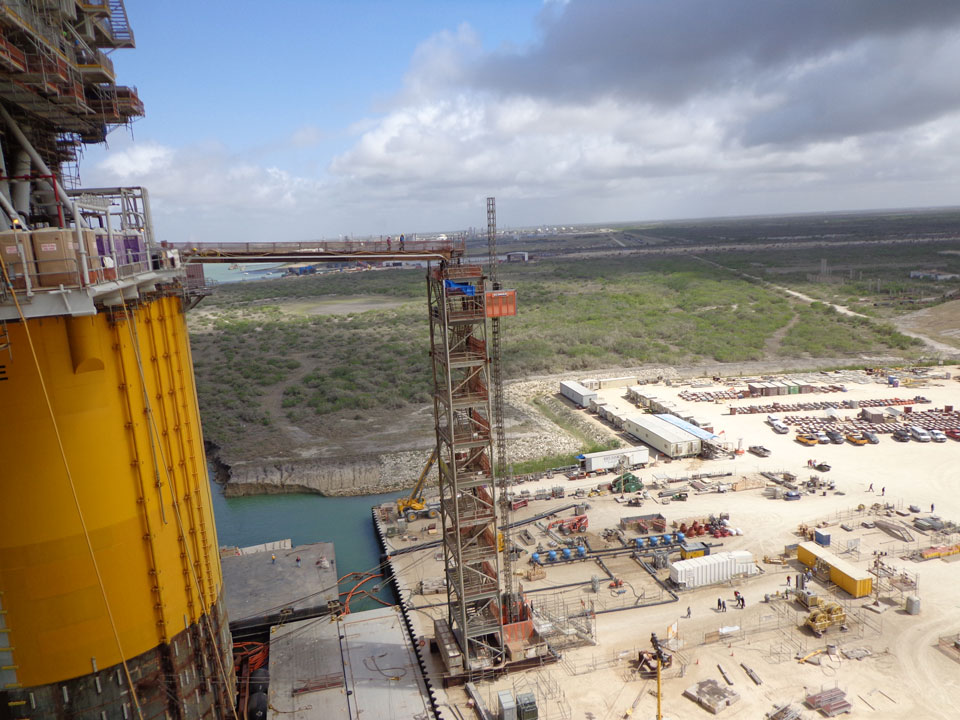
We worked with Shell from design to commissioning. Photos show the platform in the shipyard under construction.
Olympus
Gulf of Mexico
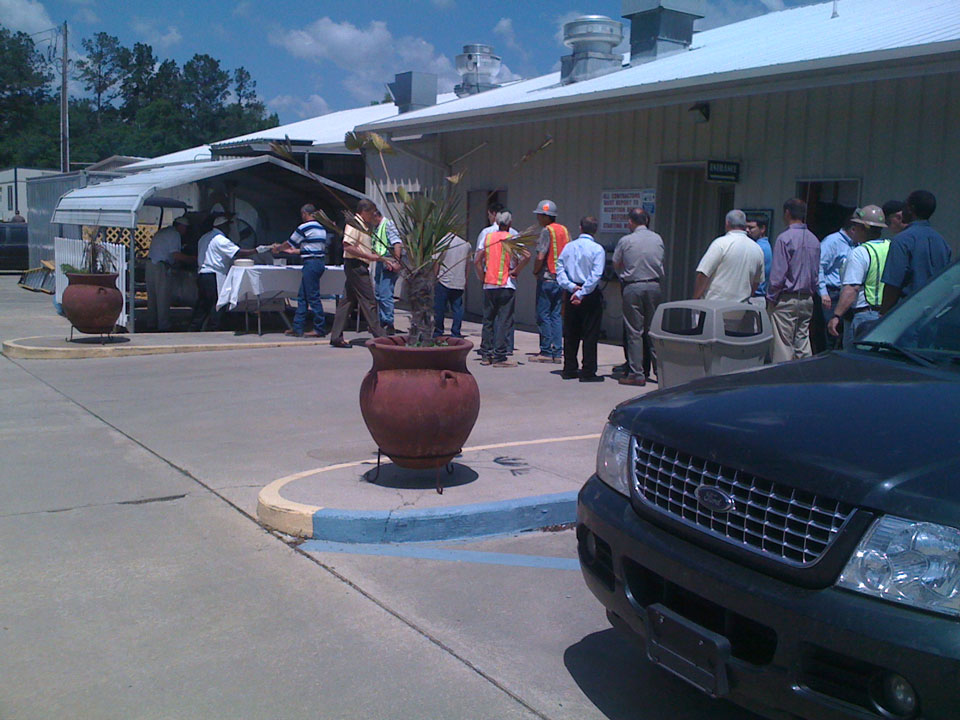
This is our emergency setup for the Deepwater Horizon response at the Shell Robert Training Center. In total, about 450 people being served 24/7 from our mobile kitchen and auxiliary serving stations.
RTC
Robert, LA
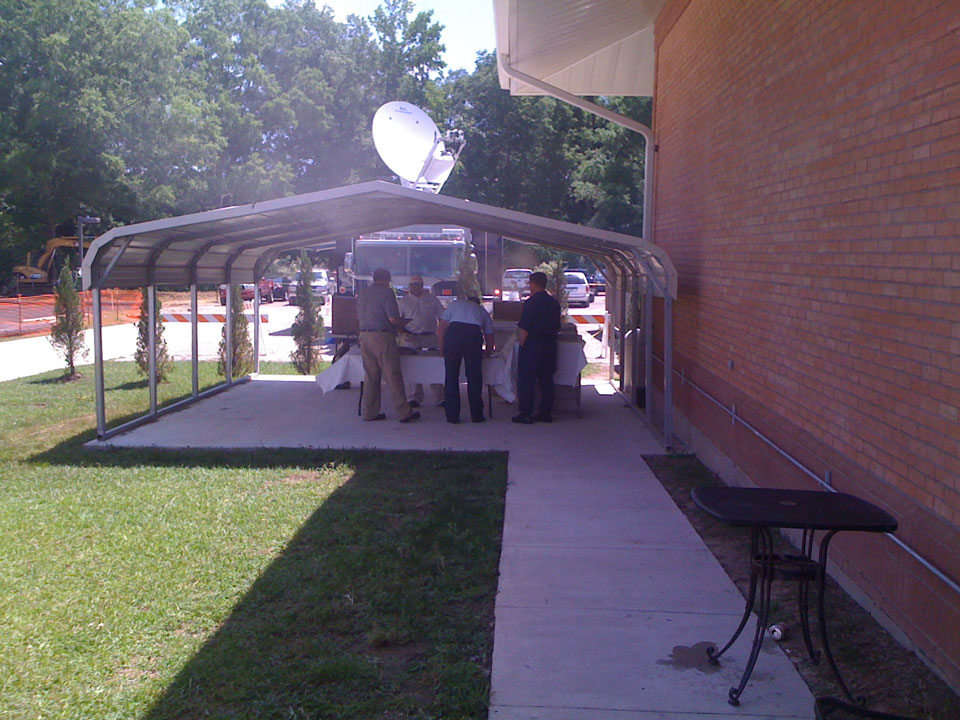
This is our emergency setup for the Deepwater Horizon response at the Shell Robert Training Center. In total, about 450 people being served 24/7 from our mobile kitchen and auxiliary serving stations.
RTC
Robert, LA
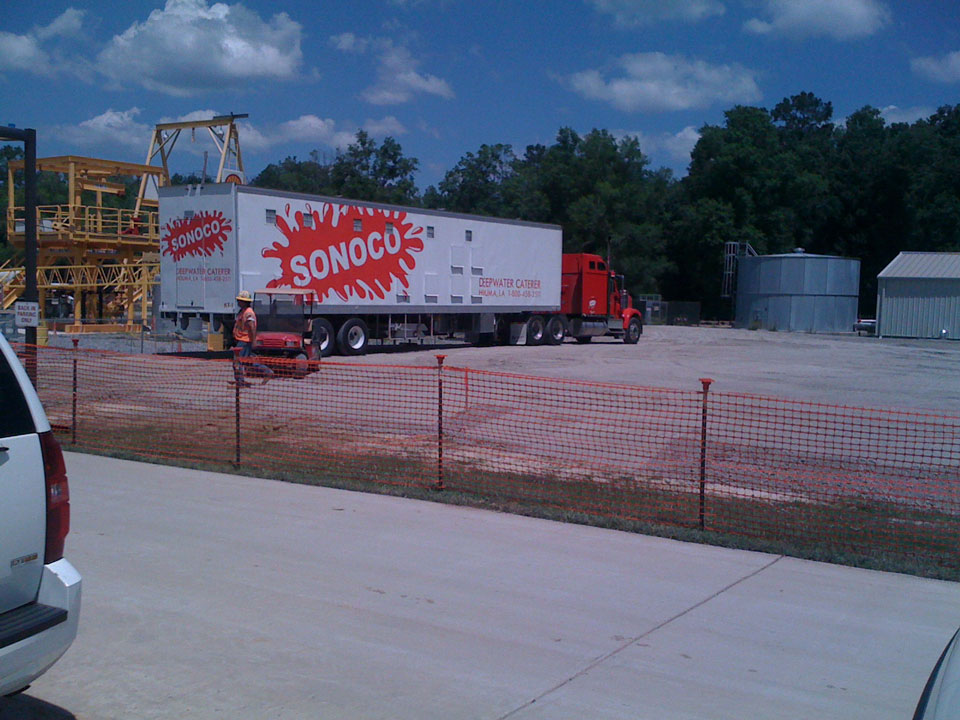
This is our emergency setup for the Deepwater Horizon response at the Shell Robert Training Center. In total, about 450 people being served 24/7 from our mobile kitchen and auxiliary serving stations.
RTC
Robert, LA
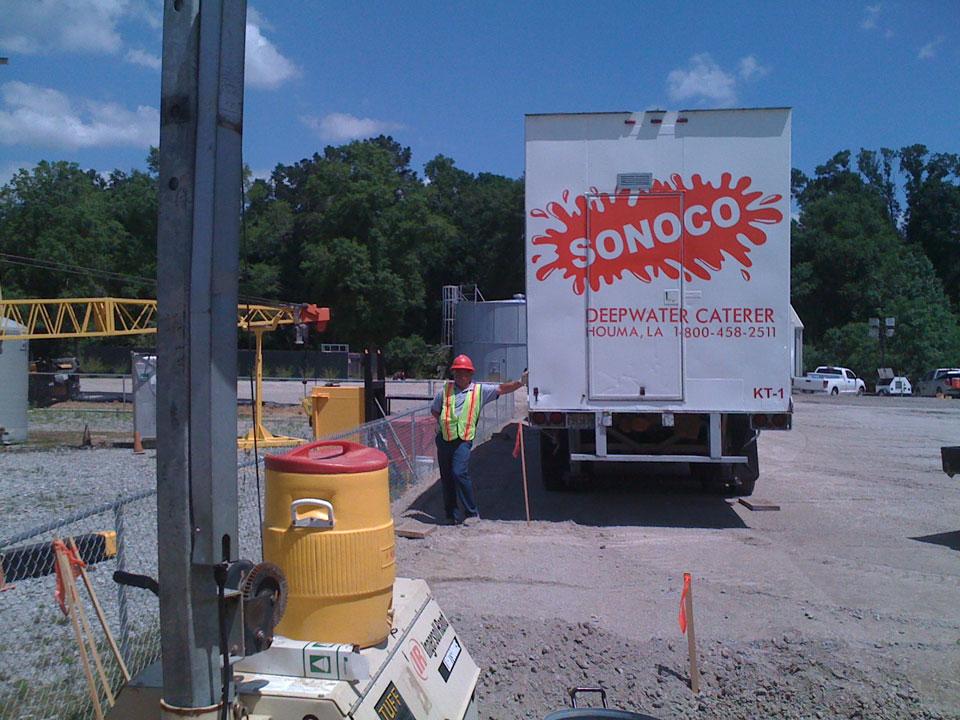
This is our emergency setup for the Deepwater Horizon response at the Shell Robert Training Center. In total, about 450 people being served 24/7 from our mobile kitchen and auxiliary serving stations.
RTC
Robert, LA
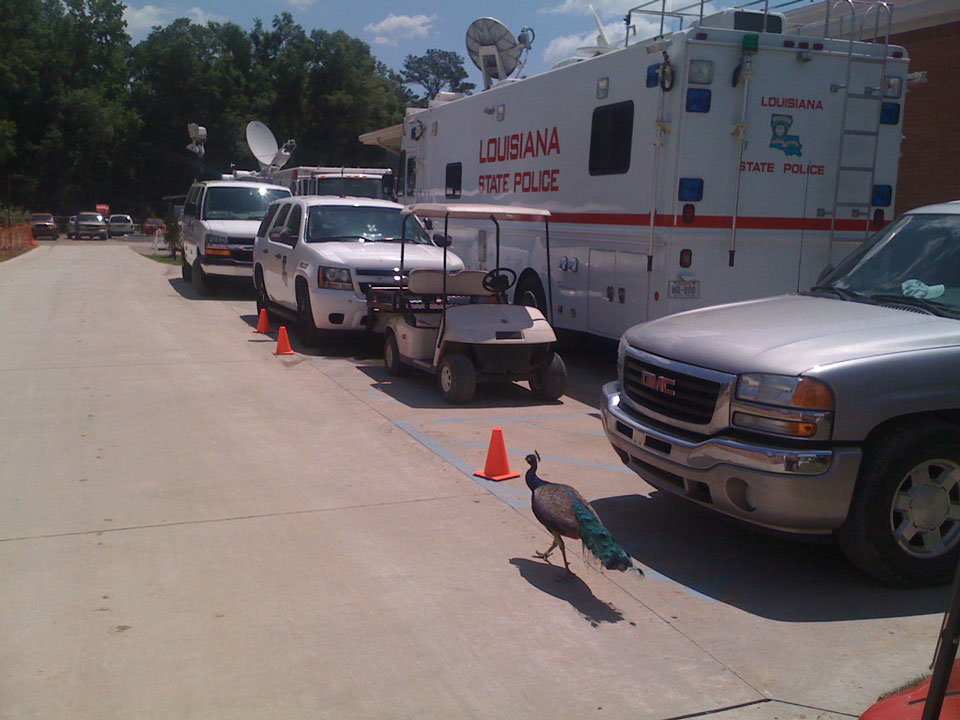
This is our emergency setup for the Deepwater Horizon response at the Shell Robert Training Center. In total, about 450 people being served 24/7 from our mobile kitchen and auxiliary serving stations.
RTC
Robert, LA
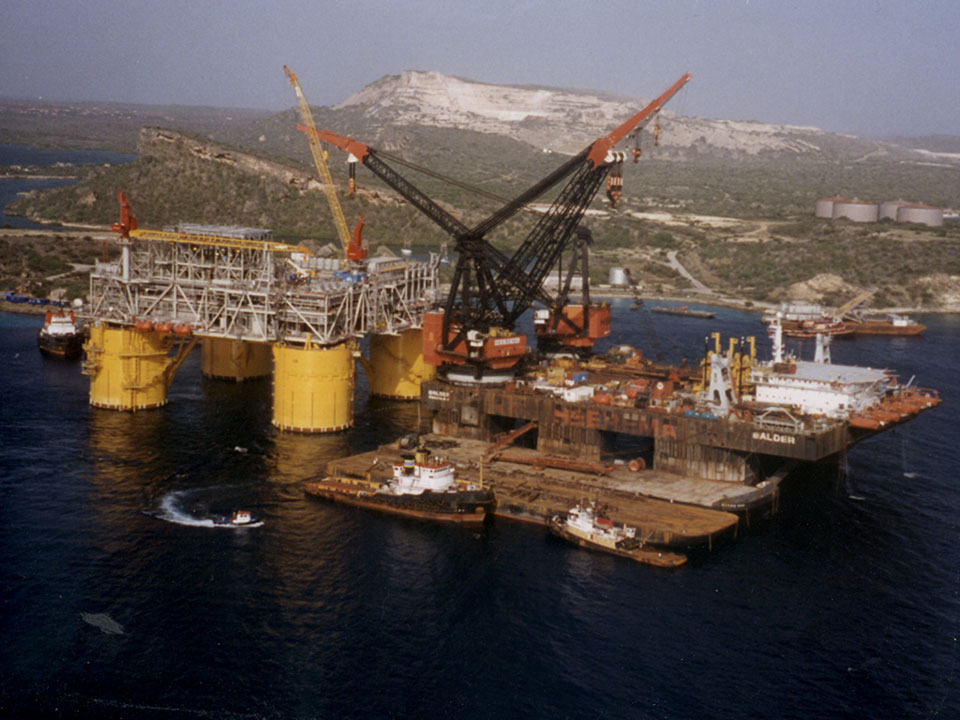
We worked with Shell from design to commissioning. Photos mostly show the TLP (tension leg platform) in Curacao, as well as the flotel (floating hotel) where about 500 were housed. We served them plus about 100 local workers.
Ursa
Gulf of Mexico
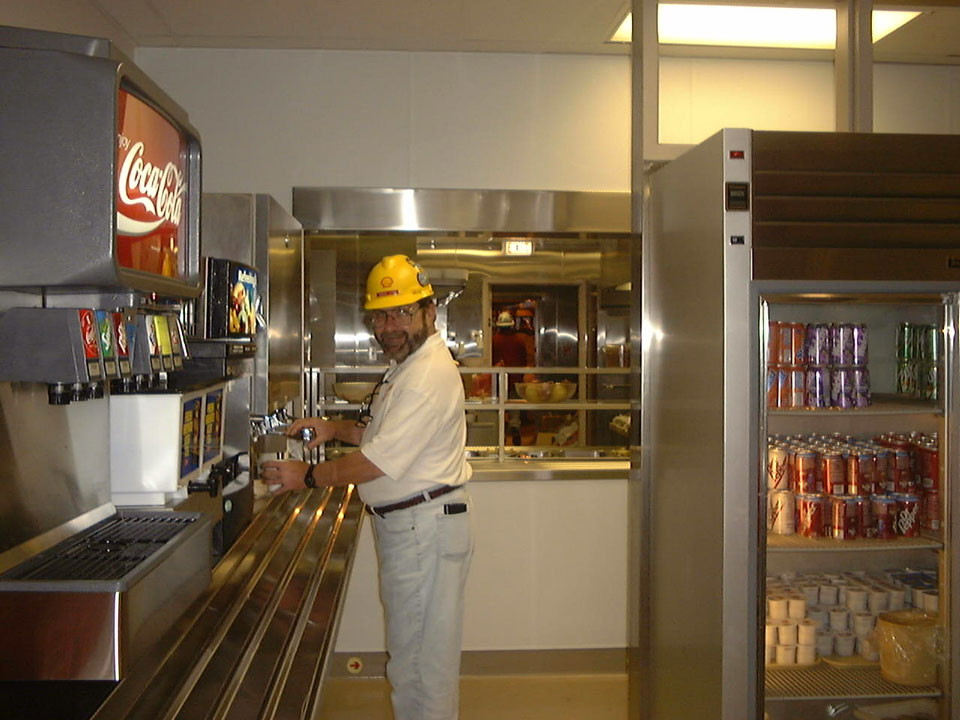
We worked with Shell from design to commissioning. Photos mostly show the TLP (tension leg platform) in Curacao, as well as the flotel (floating hotel) where about 500 were housed. We served them plus about 100 local workers.
Ursa
Gulf of Mexico
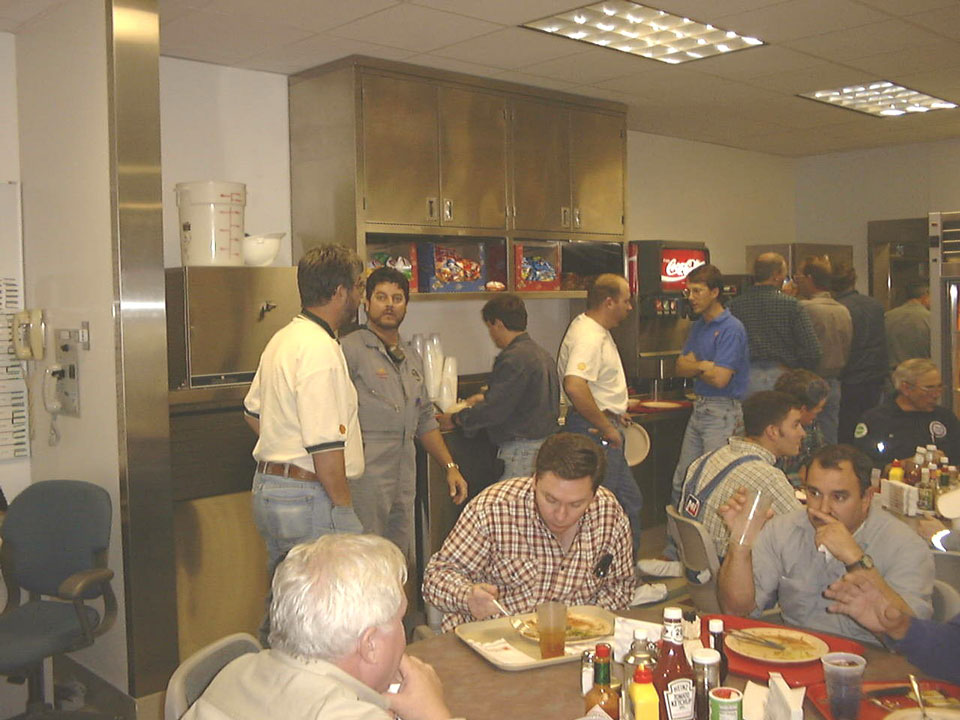
We worked with Shell from design to commissioning. Photos mostly show the TLP (tension leg platform) in Curacao, as well as the flotel (floating hotel) where about 500 were housed. We served them plus about 100 local workers.
Ursa
Gulf of Mexico
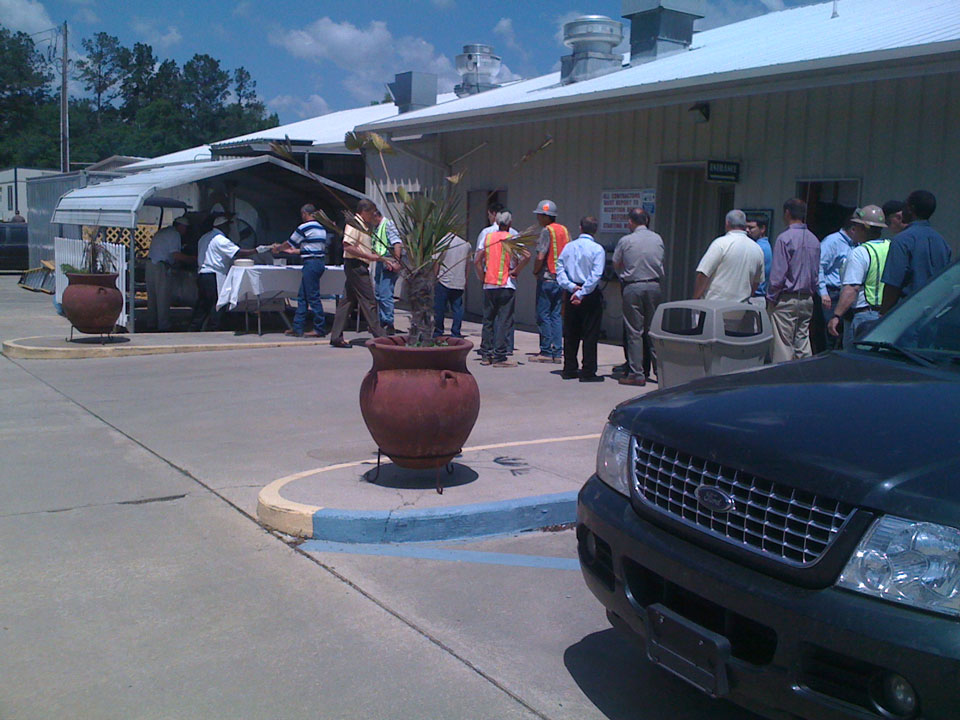
This is our emergency setup for the Deepwater Horizon response at the Shell Robert Training Center. In total, about 450 people being served 24/7 from our mobile kitchen and auxiliary serving stations.
RTC
Robert, LA
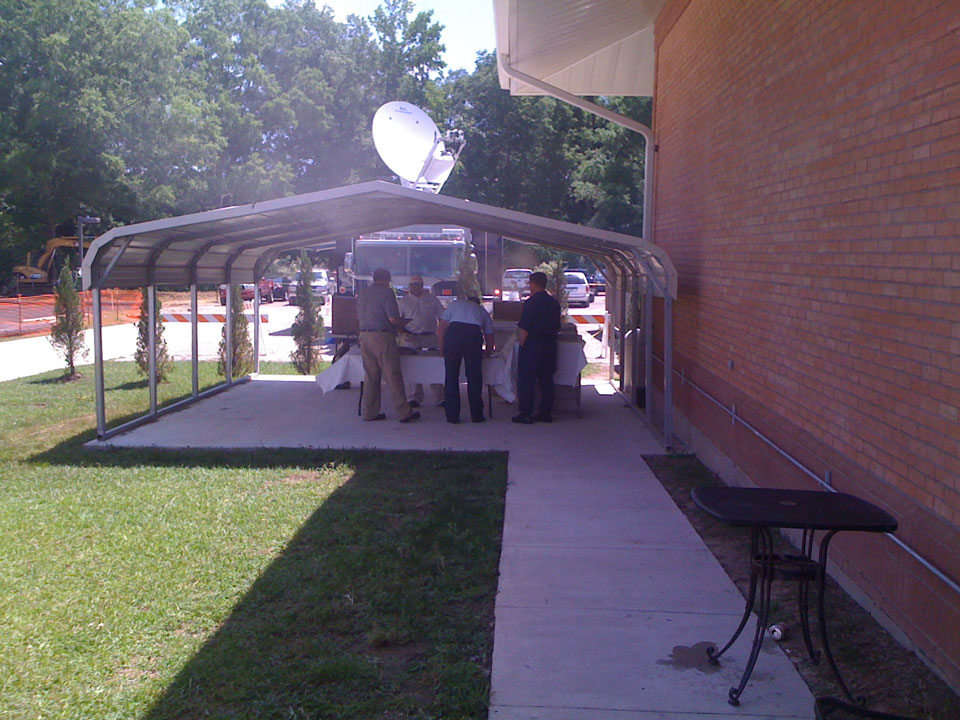
This is our emergency setup for the Deepwater Horizon response at the Shell Robert Training Center. In total, about 450 people being served 24/7 from our mobile kitchen and auxiliary serving stations.
RTC
Robert, LA
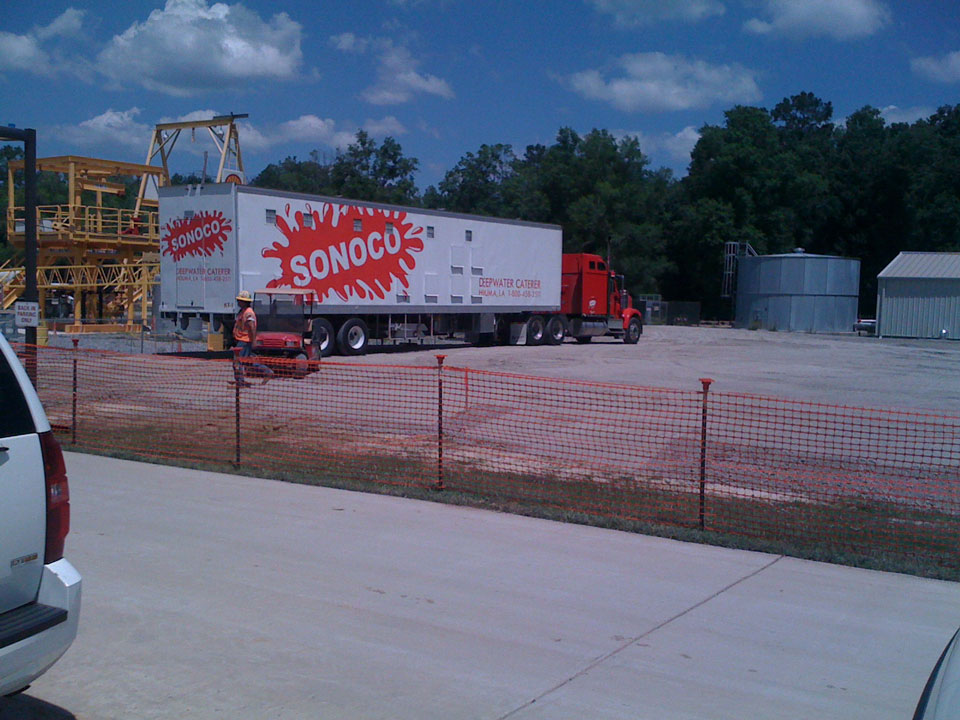
This is our emergency setup for the Deepwater Horizon response at the Shell Robert Training Center. In total, about 450 people being served 24/7 from our mobile kitchen and auxiliary serving stations.
RTC
Robert, LA
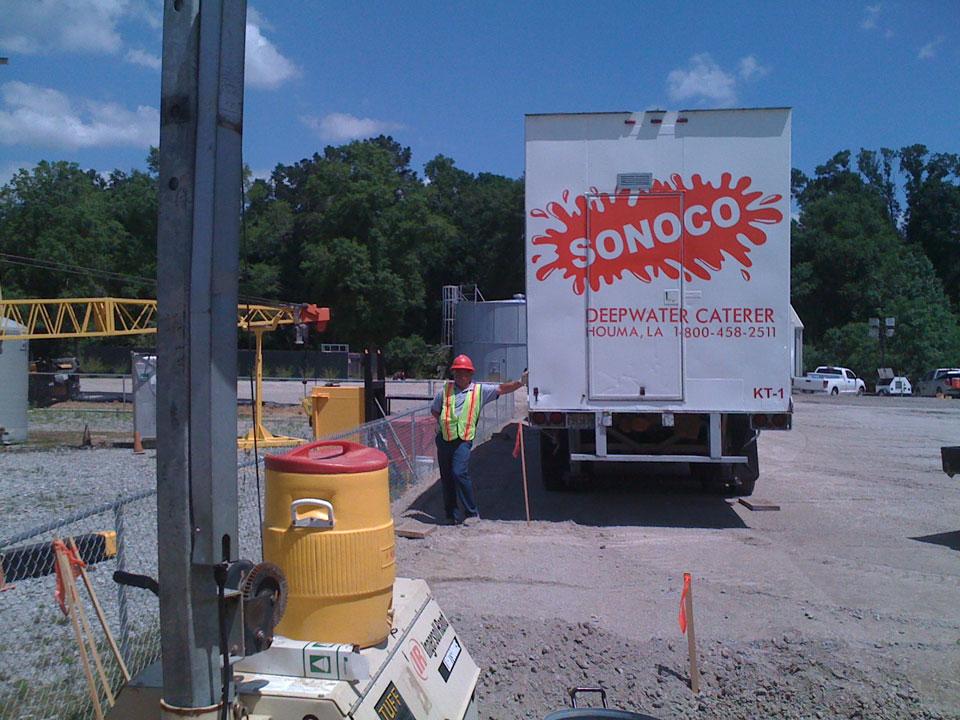
This is our emergency setup for the Deepwater Horizon response at the Shell Robert Training Center. In total, about 450 people being served 24/7 from our mobile kitchen and auxiliary serving stations.
RTC
Robert, LA
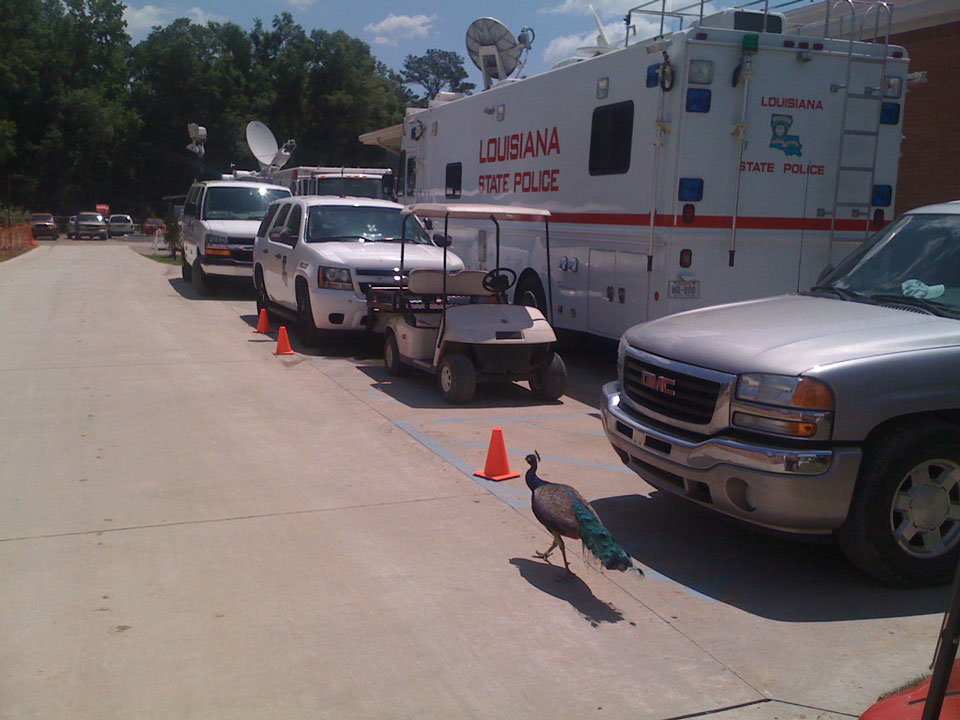
This is our emergency setup for the Deepwater Horizon response at the Shell Robert Training Center. In total, about 450 people being served 24/7 from our mobile kitchen and auxiliary serving stations.
RTC
Robert, LA
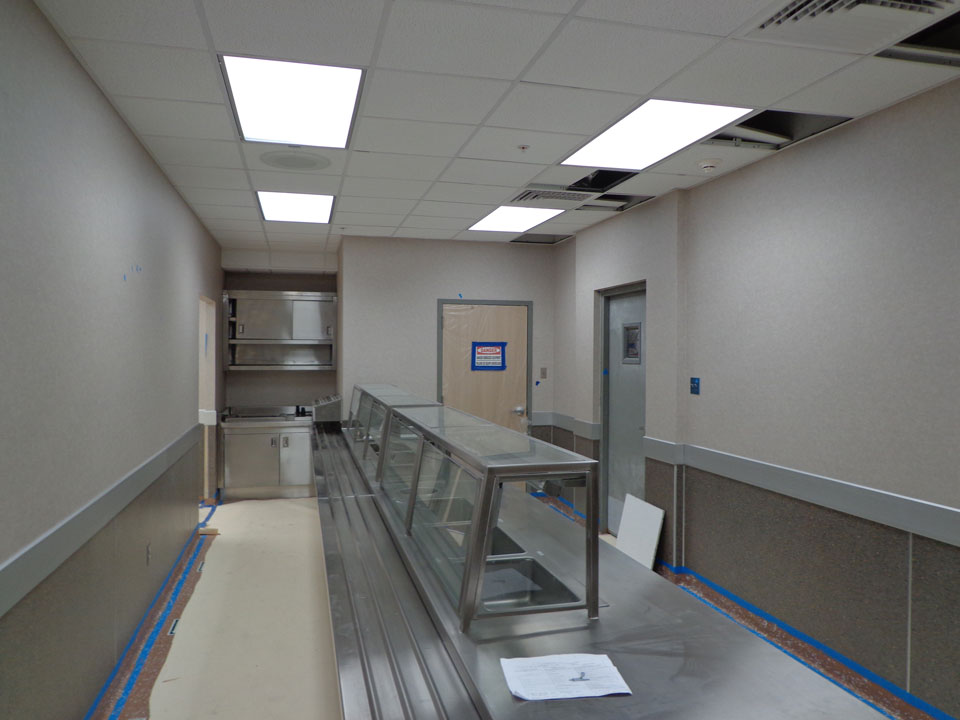
We worked with Shell from design to commissioning. Photos show the platform in the shipyard under construction.
Olympus
Gulf of Mexico
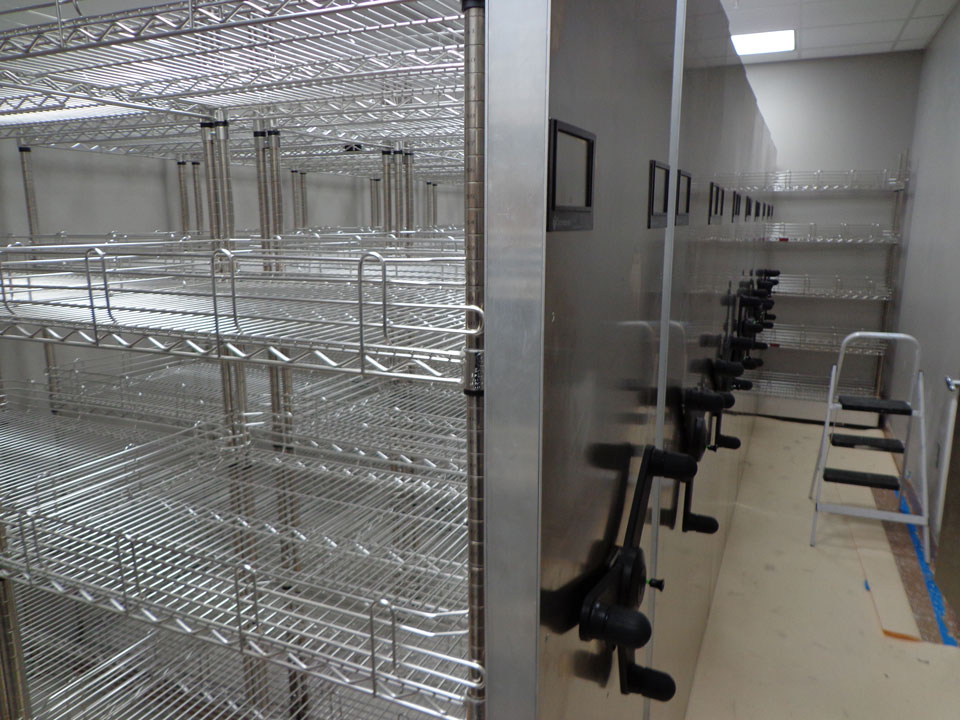
We worked with Shell from design to commissioning. Photos show the platform in the shipyard under construction.
Olympus
Gulf of Mexico
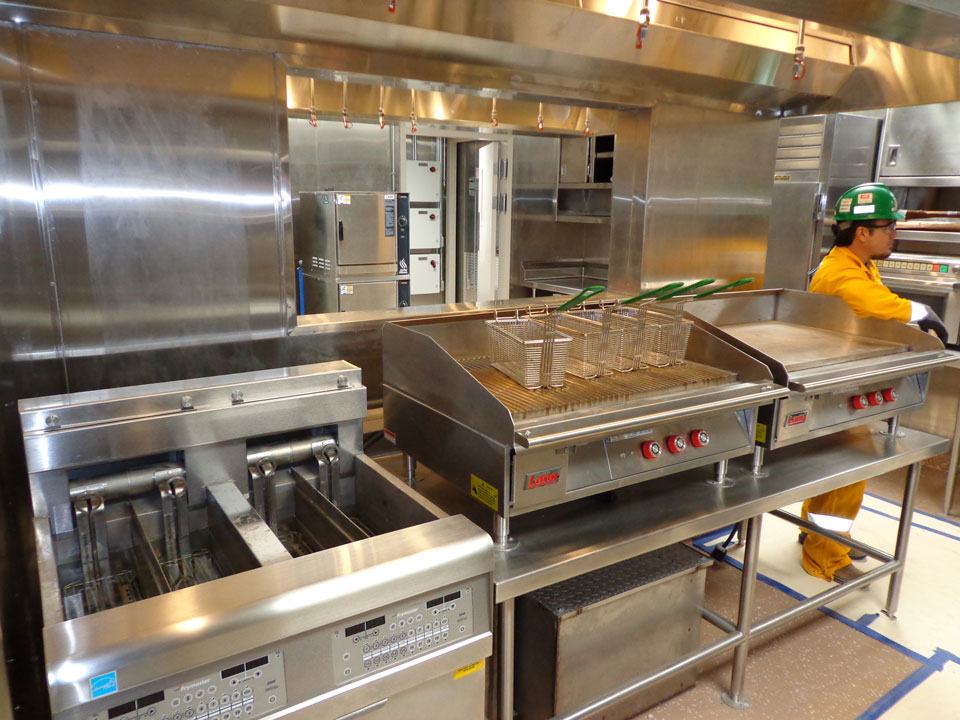
We worked with Shell from design to commissioning. Photos show the platform in the shipyard under construction.
Olympus
Gulf of Mexico
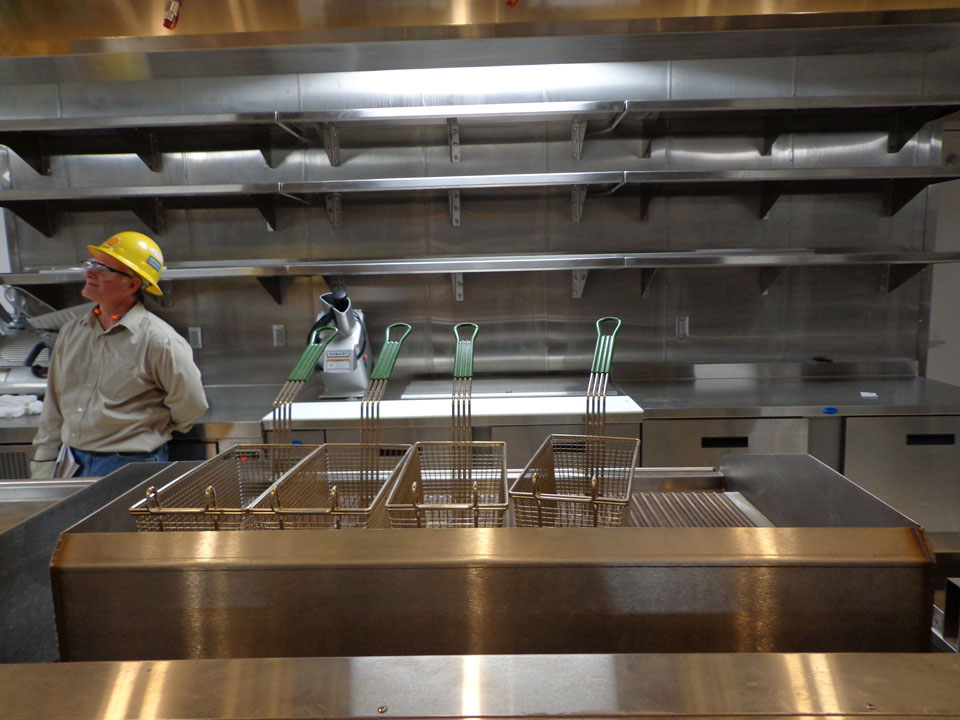
We worked with Shell from design to commissioning. Photos show the platform in the shipyard under construction.
Olympus
Gulf of Mexico
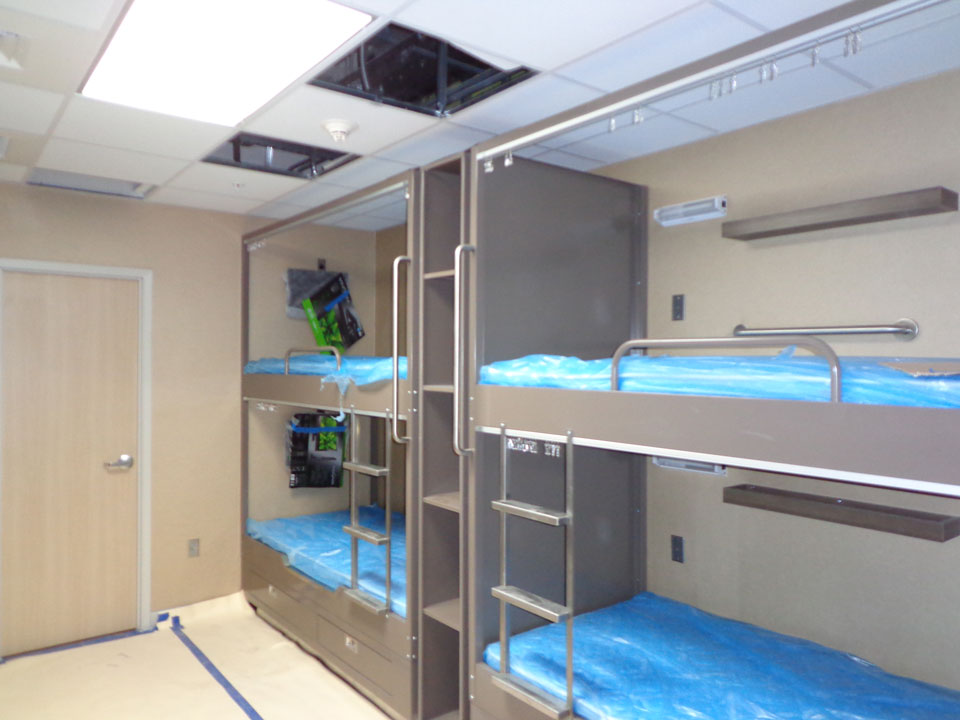
We worked with Shell from design to commissioning. Photos show the platform in the shipyard under construction.
Olympus
Gulf of Mexico
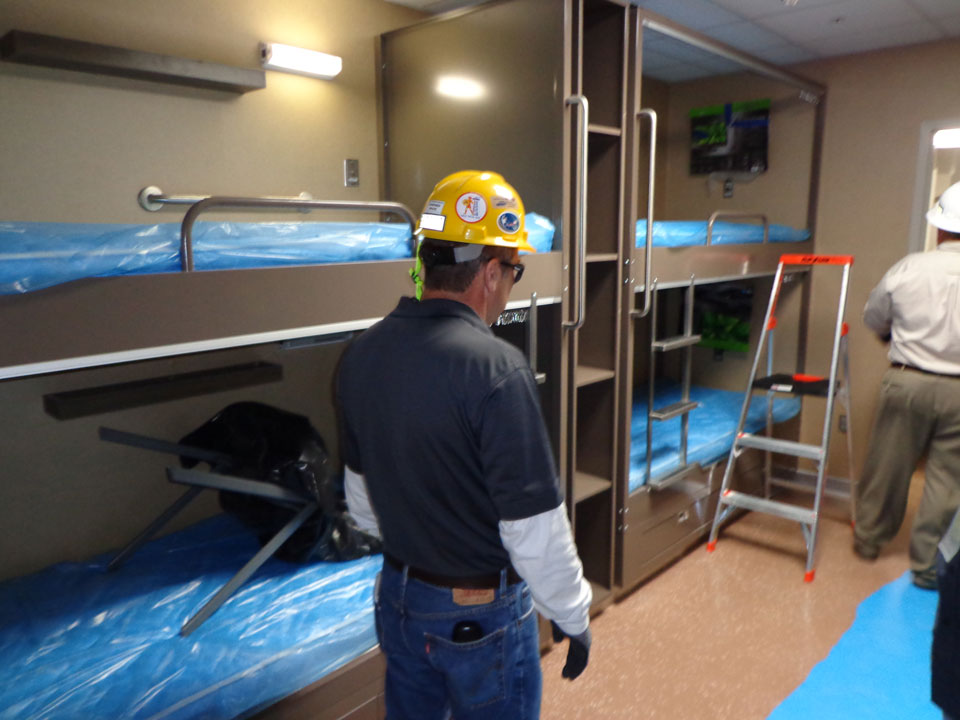
We worked with Shell from design to commissioning. Photos show the platform in the shipyard under construction.
Olympus
Gulf of Mexico
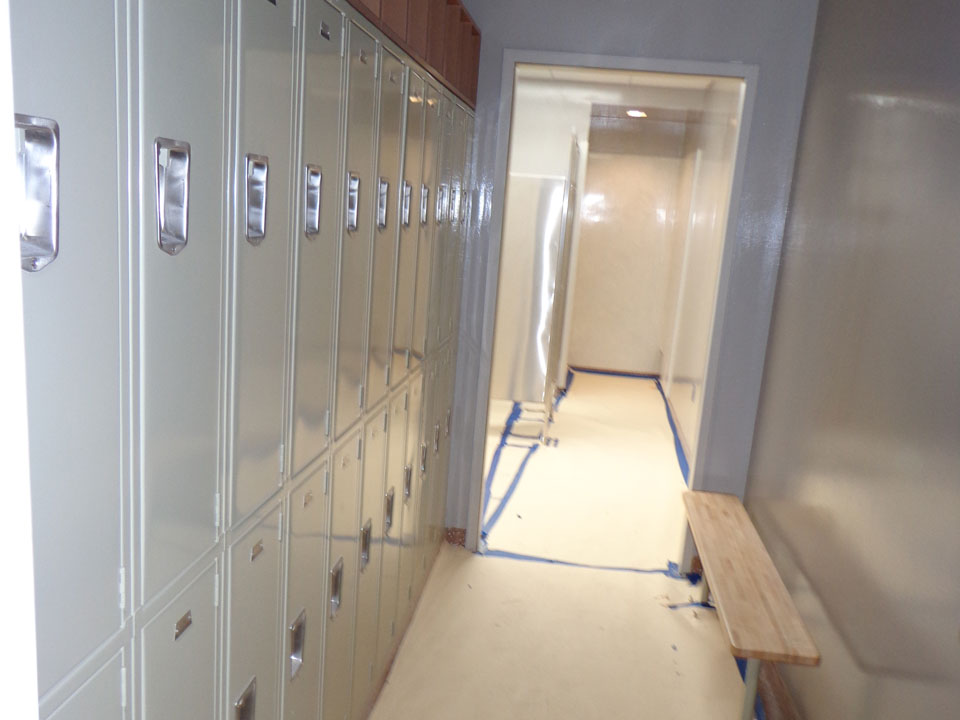
We worked with Shell from design to commissioning. Photos show the platform in the shipyard under construction.
Olympus
Gulf of Mexico
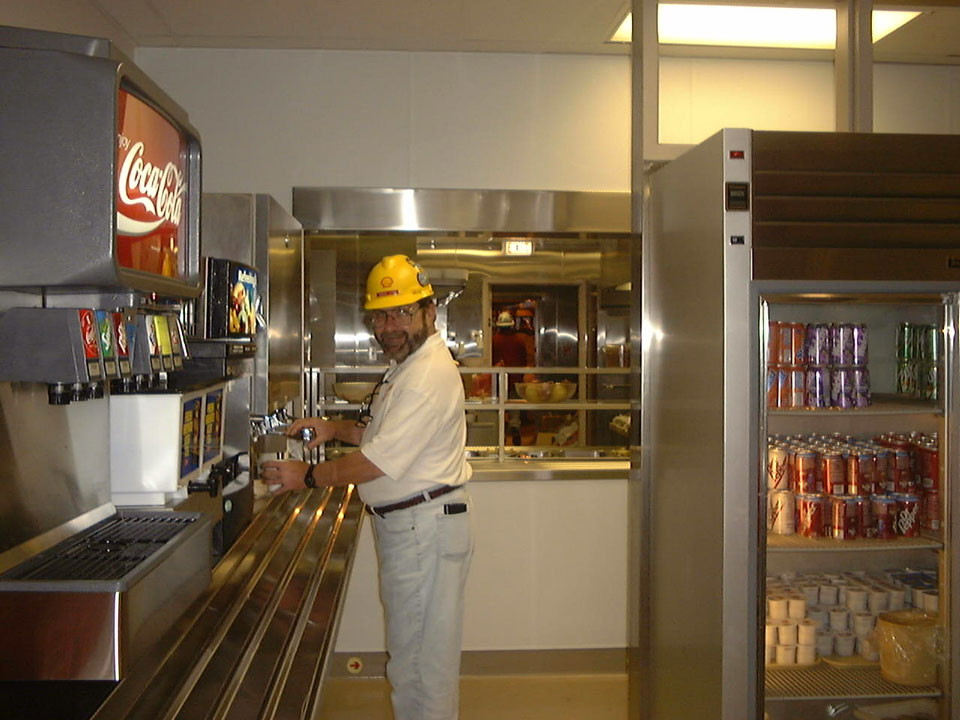
We worked with Shell from design to commissioning. Photos mostly show the TLP (tension leg platform) in Curacao, as well as the flotel (floating hotel) where about 500 were housed. We served them plus about 100 local workers.
Ursa
Gulf of Mexico
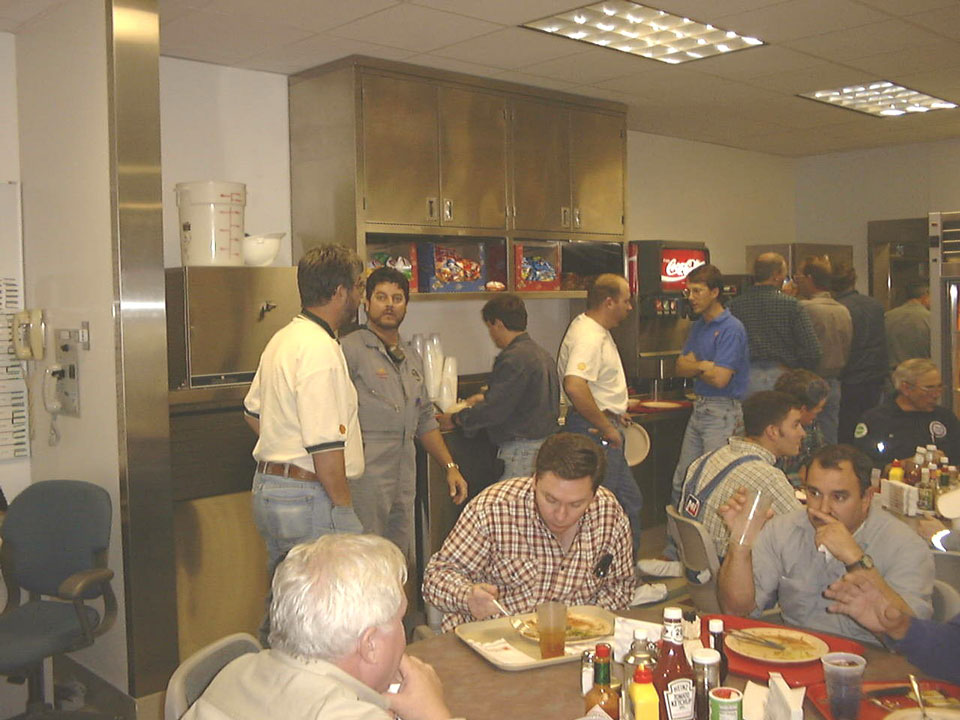
We worked with Shell from design to commissioning. Photos mostly show the TLP (tension leg platform) in Curacao, as well as the flotel (floating hotel) where about 500 were housed. We served them plus about 100 local workers.
Ursa
Gulf of Mexico
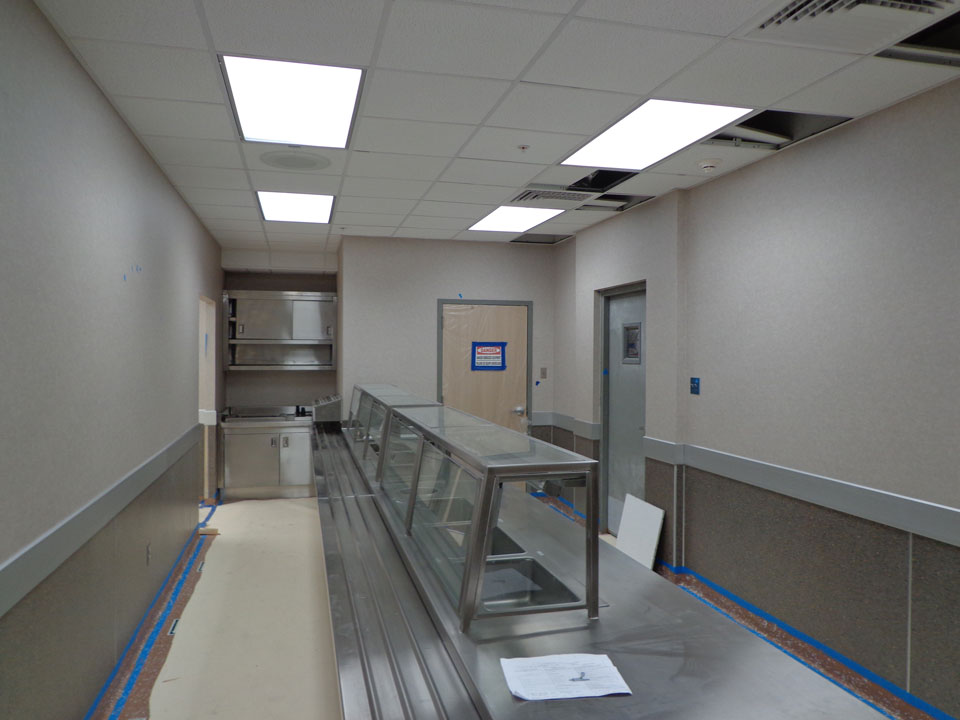
We worked with Shell from design to commissioning. Photos show the platform in the shipyard under construction.
Olympus
Gulf of Mexico
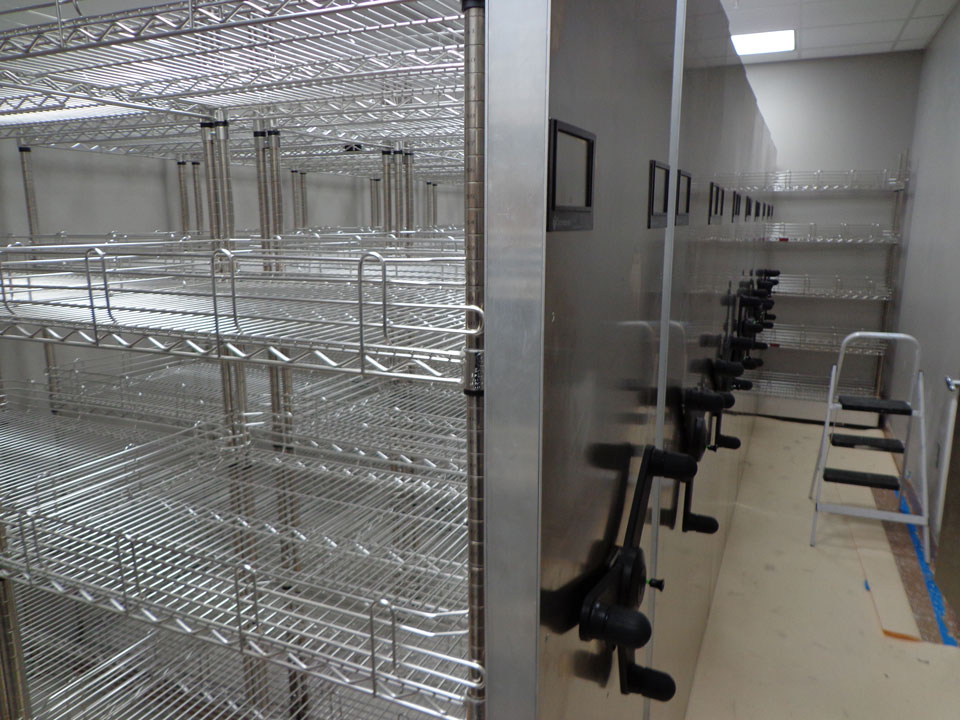
We worked with Shell from design to commissioning. Photos show the platform in the shipyard under construction.
Olympus
Gulf of Mexico
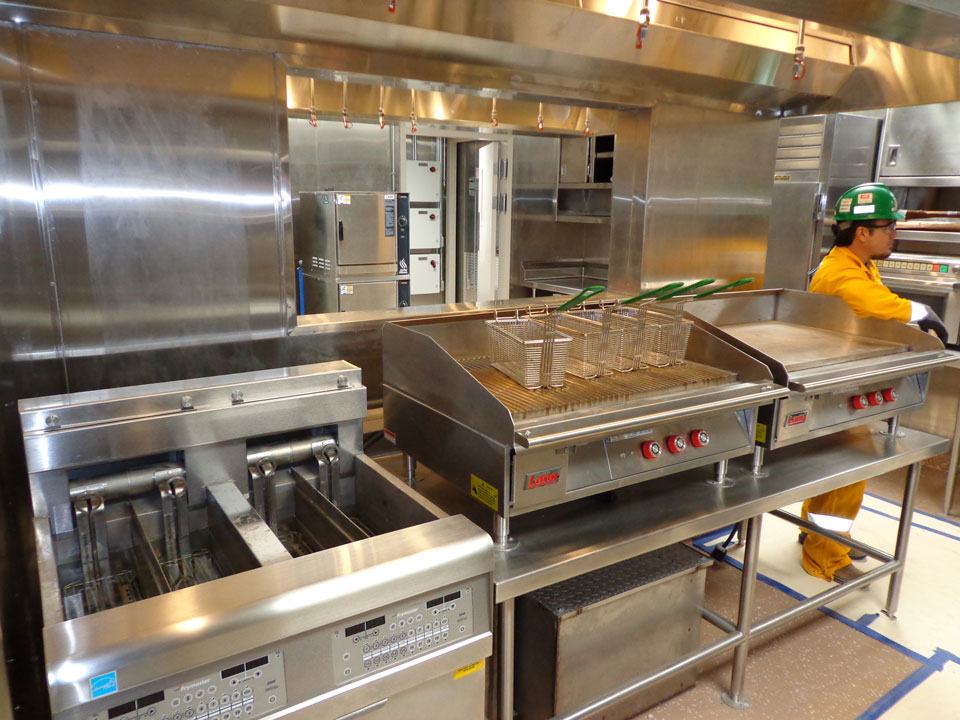
We worked with Shell from design to commissioning. Photos show the platform in the shipyard under construction.
Olympus
Gulf of Mexico
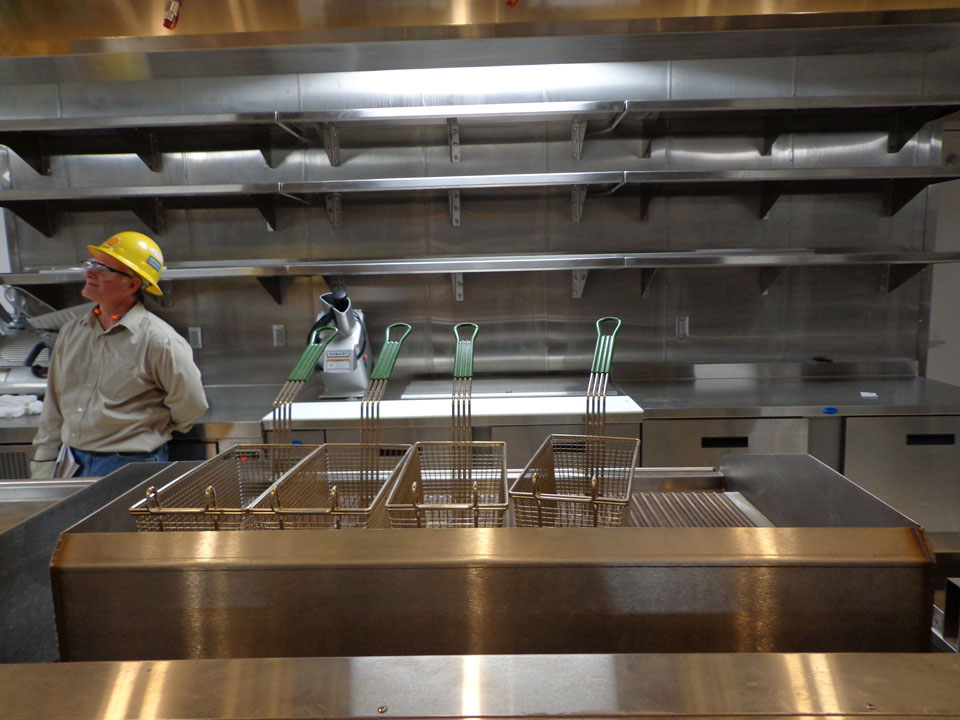
We worked with Shell from design to commissioning. Photos show the platform in the shipyard under construction.
Olympus
Gulf of Mexico
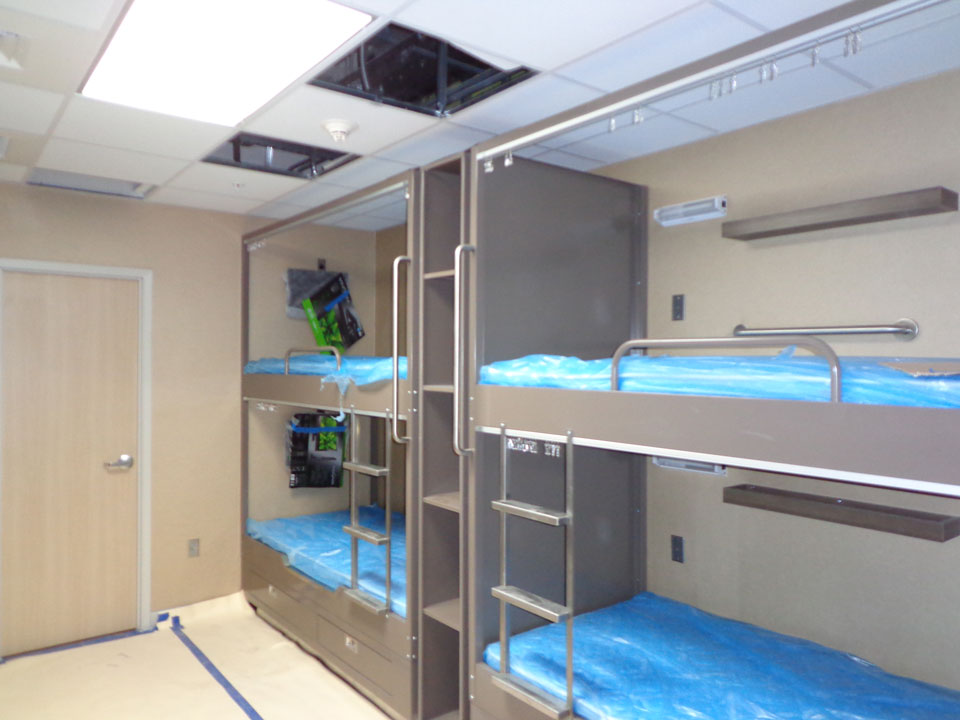
We worked with Shell from design to commissioning. Photos show the platform in the shipyard under construction.
Olympus
Gulf of Mexico
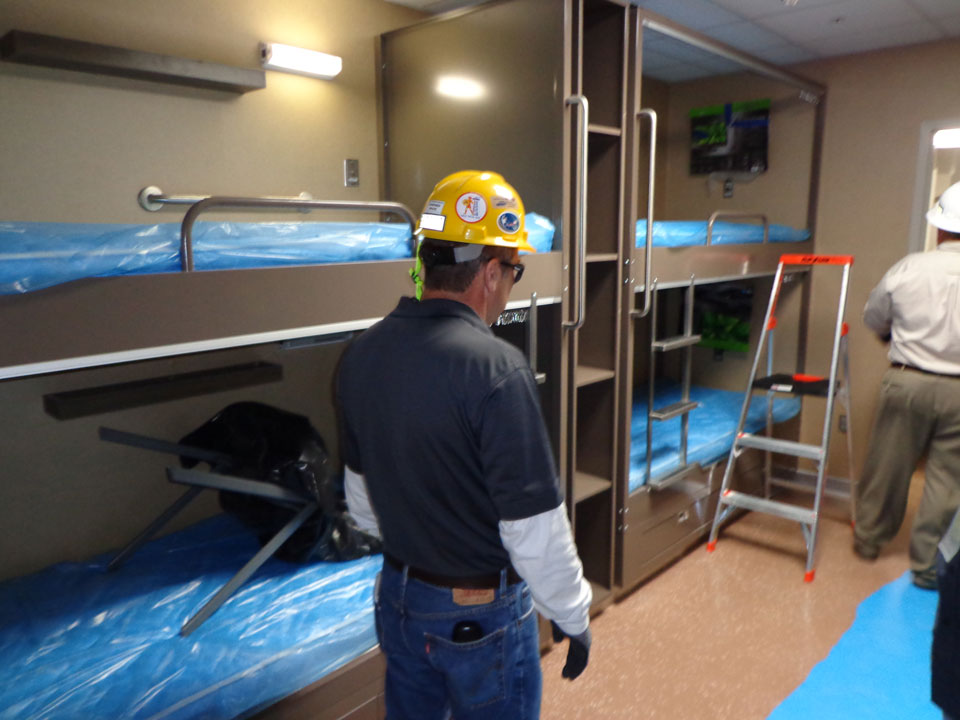
We worked with Shell from design to commissioning. Photos show the platform in the shipyard under construction.
Olympus
Gulf of Mexico
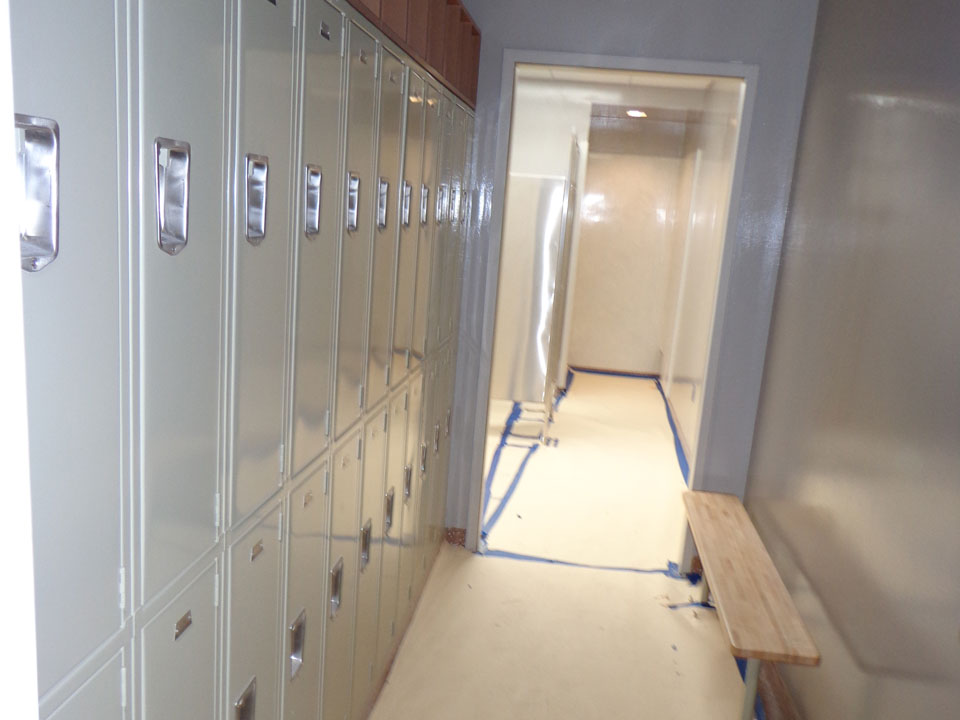
We worked with Shell from design to commissioning. Photos show the platform in the shipyard under construction.
Olympus
Gulf of Mexico
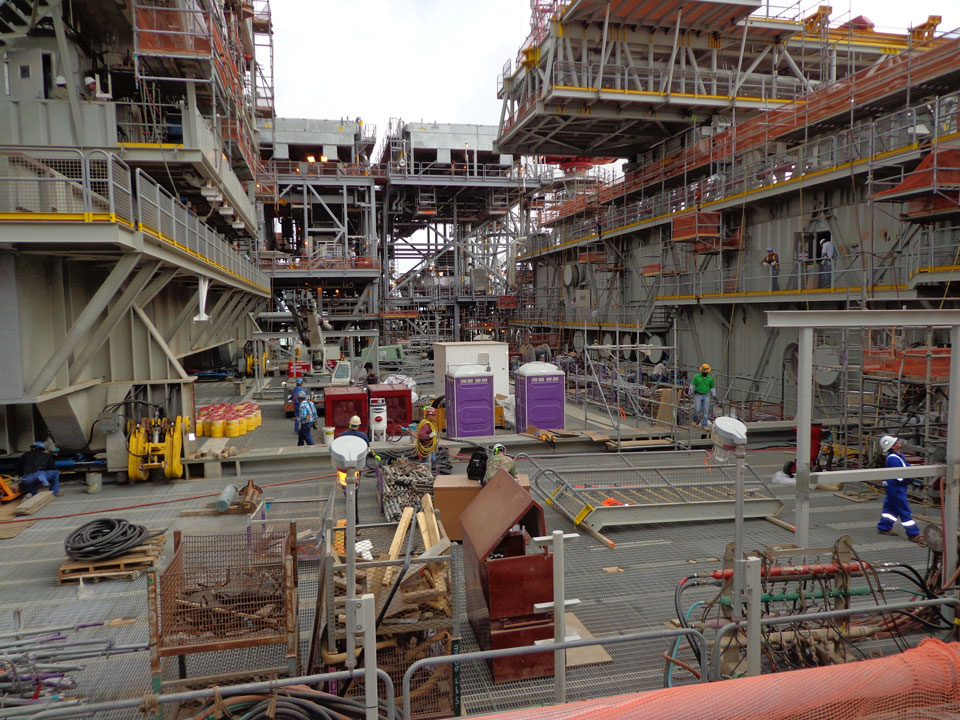
We worked with Shell from design to commissioning. Photos show the platform in the shipyard under construction.
Olympus
Gulf of Mexico
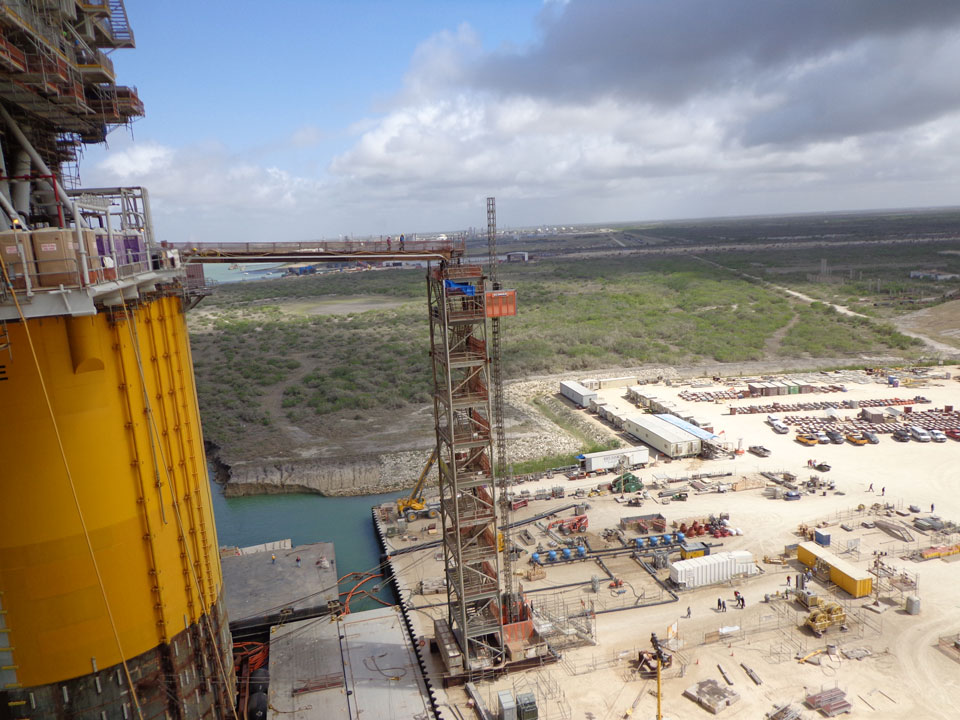
We worked with Shell from design to commissioning. Photos show the platform in the shipyard under construction.
Olympus
Gulf of Mexico
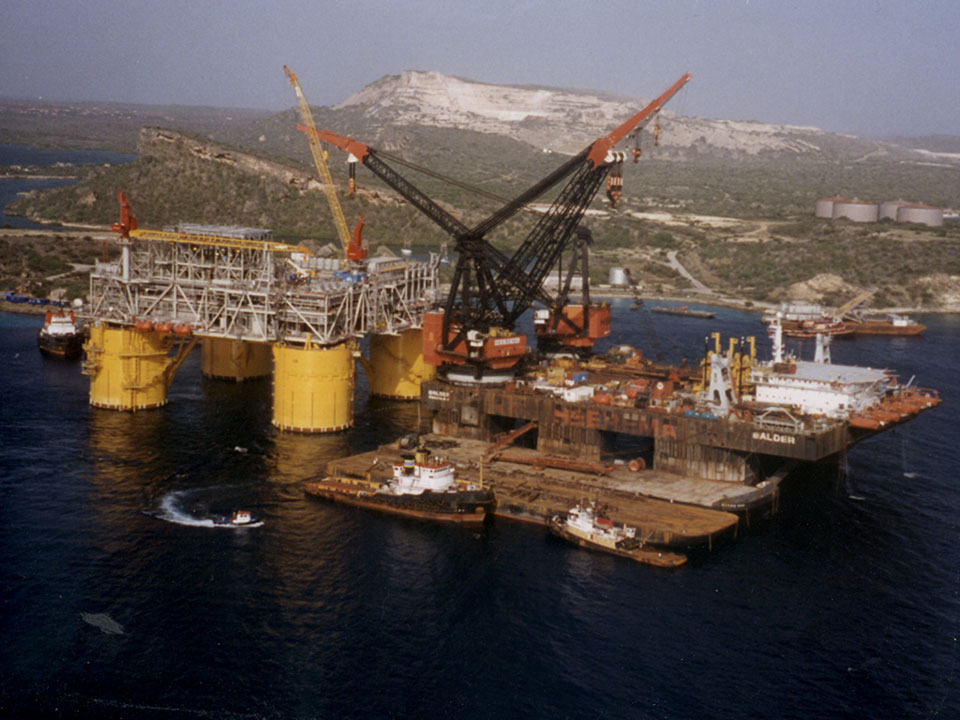
We worked with Shell from design to commissioning. Photos mostly show the TLP (tension leg platform) in Curacao, as well as the flotel (floating hotel) where about 500 were housed. We served them plus about 100 local workers.
Ursa
Gulf of Mexico
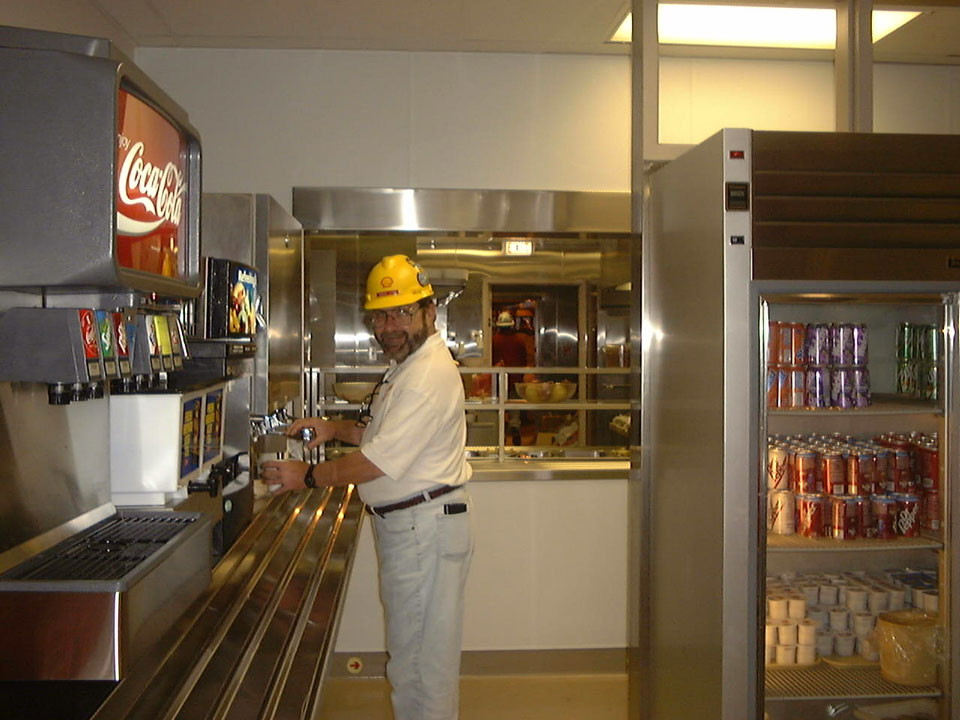
We worked with Shell from design to commissioning. Photos mostly show the TLP (tension leg platform) in Curacao, as well as the flotel (floating hotel) where about 500 were housed. We served them plus about 100 local workers.