Remote/Disaster operations
our response
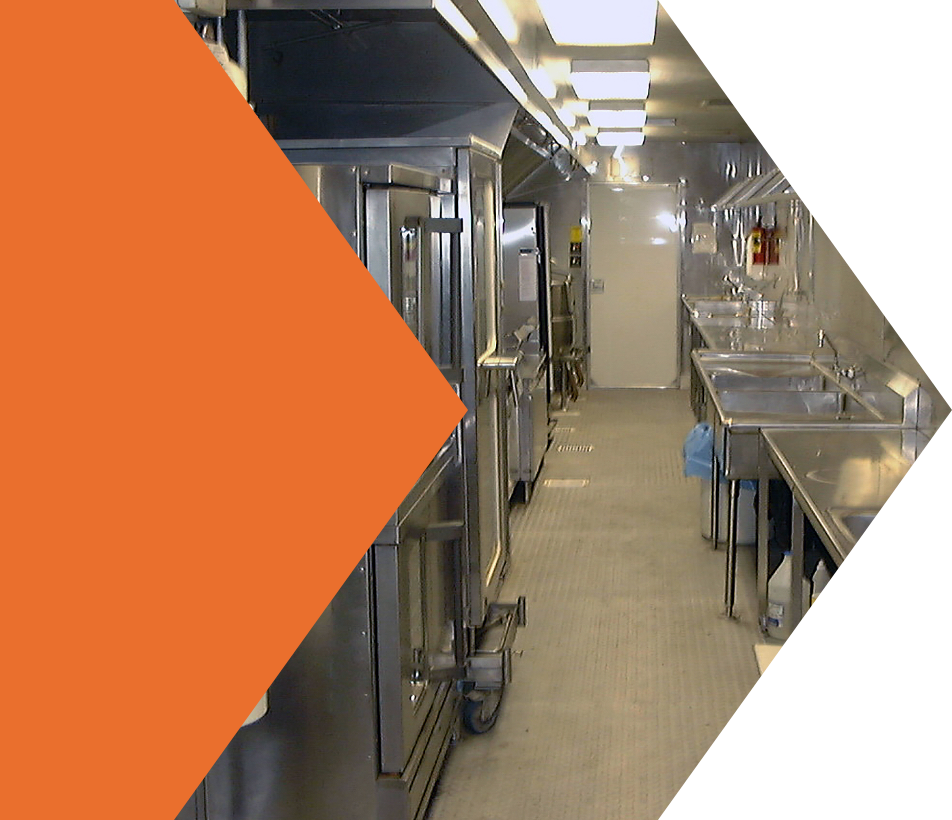
Proven performance under pressure
What do hurricanes Gustav, Katrina, and the Macando well blowout have in common? For us, it’s that for each of these disasters, SONOCO was on a customer’s location immediately after, providing emergency service for hundreds of people with our mobile kitchen and support package.
Below are some highlights of how we’ve responded to emerging situations in the past. There are many more, involving local and state law enforcement, electric co-ops and feeding emergency responders and more. In the past 35 years, we have closed for only 2 days due to hurricanes. The Monday after Katrina and the day Gustav made landfall.
We’re a 24/7 company no matter what. You can count on us.
1999: Diamond Ocean Confidence
Diamond Offshore purchased a flotel and moved it to Sabine Pass, TX where it would be converted into a world-class, high specification semisubmersible drilling rig.
The crew was housed in a couple of stacked rigs. SONOCO provided the catering on both. As the demands of the project increased, the decision was made to double the crew within a week. Supporting that number in a remote location like Sabine Pass was no small task. With Diamond’s senior management, we surveyed the area and an old Grasso dock and building were selected to set up a camp. In less than 4 days, the building was converted to housing, a dining room package installed, our mobile kitchen set up, generator package, dry storage containers and an 8 x 20 reefer and freezer installed. Groceries arrived on day 4, and we opened for business on day 6. Diamond had about 500 people on the project about a week later.
For the next year, we supported the project, serving 4 meals each day to the entire group. The mobile kitchen supported about 70% of that number. A month into the peak staffing levels, Diamond asked us to help solve the problem of long mealtimes. The workers had to come off of the rig and wait for the shuttle buses to take them a mile away to the galleys. The solution was simple: Move the meals into the yard next to the rig.
We moved a mobile office unit closer, set up utilities and brought in equipment, tables, chairs and beverage dispensers. Less than a week after the decision was made, we were running a sub shop serving customers a terrific selection of sandwiches made to order. This shaved almost half an hour off of meal times. Multiplied by the number of workers, it saved over 1,000 hours each week! That’s the equivalent of an extra 25 workers.
Late in 2000, the Ocean Confidence successfully completed sea trials and went to work. We packed up shop in Sabine Pass and began service aboard the rig.
August 29, 2005: Hurricane Katrina
Hurricane Katrina made landfall and tore its way across the region. The Shell Training Center in Robert, LA became a shelter of for many employees who began arriving before it made landfall. Within days, the center was overflowing with employees who had no place to go to live or work. New Orleans was under water and Shell Square was out of commission.
Only a day or two after Katrina passed, we had our mobile kitchen on site. Additional staff reported and we began serving a group that grew from 100 to over 500. We operated at “Camp Robert” for nearly a year, serving Shell’s employees and emergency response teams that they hosted; including law enforcement, fire and rescue and others from Arizona to New York state.
As Christmas approached, Frank Glaviano asked us to determine the feasability of putting a foodservice operation into One Shell Square. The building was only a couple of weeks away from being able to open, but there was no place in the area for anyone to eat. This was an absolute must if they were to bring their 1,000 employees back to New Orleans.
A couple of days after meeting with Frank, we all went up to floor 11 at OSS and worked out a plan with Robert Olivier from Waldemar S. Nelson. Within days a plan was in place, permits granted and trades were busy turning an empty floor into dining for 500 people, a holding kitchen, coffee shop, storage and an assembly / presentation space with seating for those 500.
Three weeks after the project was proposed, the construction was finished. 20,000 square feet of empty space was now a friendly, inviting space with carpeting, finished spaces, the coffee shop and a servery with 8 separate buffet stations. We opened on day one serving almost 1,300 people for breakfast and lunch. We prepared the meals in a restaurant down St. Charles Avenue and delivered food continuously in specially outfitted vans. The OSS dining room closed in the fall of 2006, as the city returned to “normal” and was able to support downtown office workers.
2008: Hurricane Gustav
After Gustav made landfall in Houma, we deployed our mobile kitchen to provide operations support for the Louisiana State Police. We’ve had a long relationship with the LSP, and Troop “C” called on us to assist them with providing meals for well over a hundred officers from outside the area.
We were up and running 24 hours after the request, serving meals – mostly carryout for troopers on rescue, watch or patrol duty.
April 2010: Macando
In April 2010, Shell’s Robert operations became the focus of another disaster response effort. This time it was the Macando blowout. Within 24 hours of the blowout, Shell had offered their facility to BP and Transocean to coordinate the response team that ultimately included an inter-agency group of civil and military personnel. MMS, USCG, the US Navy, multiple law enforcement agencies, and the Army – all told, nearly 600 people were working at the center at the peak of an operation that was headed by Rear Admiral Mary Landry, USCG.
Early on, we once again set up operations to supplement our existing service. The mobile kitchen once again on site and operating 24 hours a day for weeks. We worked with multiple teams, providing normal meal service as well as numerous special services for visiting officials: US and State senators and representatives and the governor of Louisiana among others.
Some weeks later, when the team at Robert disbanded, we were asked to set up a facility in Amelia. A large team was being being deployed to run a decontamination station for vessels involved in the blowout; supply, response, and other oilfield units would be served there.
A little more than two weeks later, the camp was ready. We had our equipment in place; a large, closed tent with HVAC was set up, with capacity to seat 250 people. We ran 24/7 for weeks until the decontamination process completed.
2020: The COVID Pandemic
During the initial lockdowns across our region, Oxy committed to keeping its people safe even if it took extraordinary measures.The challenge of keeping people safe came down to preventing COVID-positive people from going offshore. The only way to do this was to isolate and test before allowing anyone to go out. It meant being able to provide everything required for hundreds of people every week.
They secured two hotels in Houma and another in Lake Charles and arranged for onsite testing to be done by their own teams. Personnel would arrive early, be tested and stay in quarantine before going to work. Hotel staff was kept to an absolute minimum to prevent casual traffic, and Oxy asked SONOCO to provide the foodservice and dining for their employees. We provided mobile kitchens for both Houma and Lake Charles. Dining services were handled entirely by us, as no outside personnel were permitted in the hotels. Our employees were tested and quarantined and we did not have a single COVID-positive employee.
We set up buffet lines for service. Three meals a day plus snacks and beverages available 24/7. Meals were served by masked SONOCO employees from the buffet. Disposable dinnerware and cutlery, preportioned salads, soups and desserts as well as packaged snacks were provided along with a traditional breakfast and full dinner every evening.
In Houma, we had two hotels to serve, and to minimize the cost, we set up a delivery route from our Mobile Kitchen to the satellite hotel (which frequently house 100 people). Meals, snacks, water, sodas, paper supplies and more were delivered four times daily, rain or shine. We continued to provide this service for nearly a year. The only downtime was during evacuations for several storms. Still, we were up and running and ready to go the day after hurricane Laura made landfall: our mobile kitchen was fine, the generator ready to go and all we needed were customers! They arrived soon after, returning to a city essentially without power.
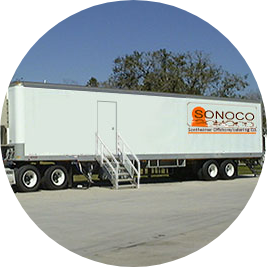
Specifications
Specifications
Dimensions (L/W/H): 53’ x 8’ x 13’6”
Generator, 50kw, multi-phase, trailer mounted
Fuel: Generator, Diesel, Kitchen, Propane
Propane: 800 lb tank, trailer mounted
Water supply: standard household supply, threaded faucet
Hot water: tankless, propane high flow
Fire Suppression: Ansul automatic hood system with fusable links and manual override.
Manual ABC class 30 pound tanks also supplied.
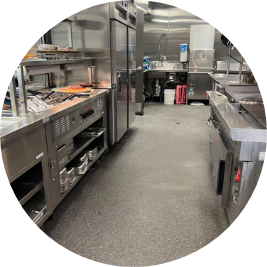
Equipment
Equipment
All equipment NSF Approved
Insulation: Harsh environment, includes Alaska
Refrigeration: 8’ x 7’ walk-in cooler
Steam Kettle, 55 gallon
Range: gas, commercial 6-burner with 24” griddle
Fryers: gas, dual 50 lb, high BTU floor mount with fry station
Steamer: dual compartment, low pressure
Ovens: gas, convection, double stack full size, 6 pan cap.
Mixer, Hobart 12 quart
Tilting Skillet: gas, 40 gallon, electric lift